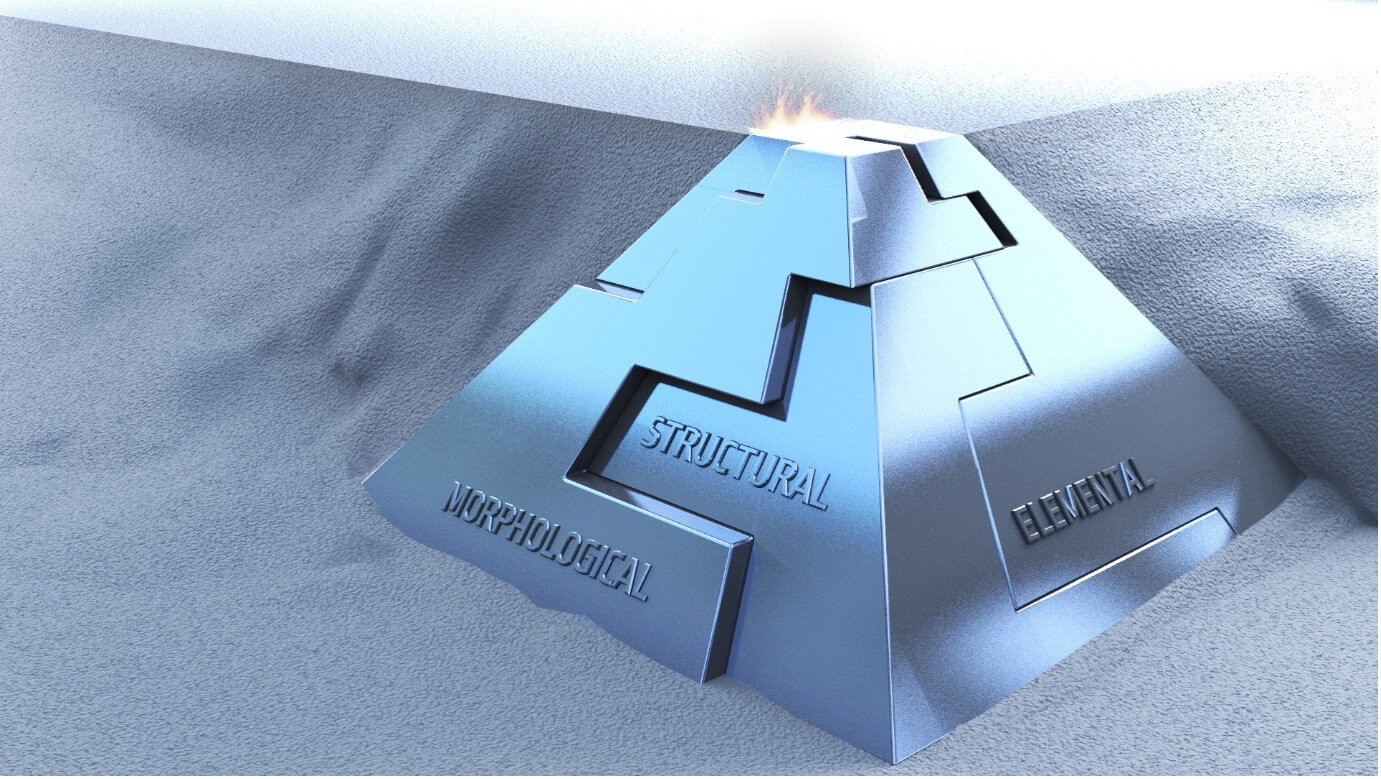
Abstract: Use of recovered powder led to a slight variation in the phase content of parts; while the chemical composition was consistent. All parts contained an excess of γ’’ phase compared to conventional Inconel 718. The most reliable monitoring of parts would incorporate both phase analysis and residual stress analysis. For this reason, all measurements were collected using the multipurpose automated Empyrean Series 3 diffractometer with MultiCore optics. All optics on this system are motorized and computer-controlled, allowing for dynamic reconfiguration of the system without user intervention. As an example, parts were analyzed using Bragg-Brentano divergent beam geometry for powder diffraction, line focus parallel-beam geometry for iso-inclination residual stress analysis, and pseudo-point focus parallel-beam geometry for pole figure (texture) analysis. The Empyrean Series 3 diffractometer with MultiCore optics can collect all 3 measurements from each part by automatically changing the optical configuration for each measurement. Powders could easily be introduced into the sample queue with the optimal configuration defined and automatically incorporated into their measurement.
Electrodes used in lithium-ion batteries have a defining influence on their electrochemical performance and are typically manufactured by coating a metal foil substrate with a multi-component slurry made of active electrode particles and conductive additives suspended in a binder solution. Size and shape distribution of electrode particles influences not only the rheology of this slurry in terms of its stability and ease of application, but also defines the quality parameters of the resulting coat like thickness uniformity, packing density and porosity. These, in turn, impact key battery performance parameters, such as ion transfer rate and battery recharge time.
The manufacturing of electrodes for lithium-ion batteries is a complex, multi-step process and presents a significant optimization challenge. Comprehensive analytical characterization with a range of complementary techniques provides a secure foundation for tackling this challenge, bringing value to both the individual components and the multi-component streams. All the techniques reviewed here have a place in the analytical toolkit for battery electrode manufacturers and all can play a vital role in meeting the targets of optimal production efficiency coupled with desirable electrochemical performance.
This study demonstrates that fast non-destructive testing using X-ray fluorescence (XRF) and X-ray diffraction (XRD) has the sensitivity necessary to detect minor variations of consequence in parts and recovered powders used in near-net-shape production with Inconel 718.