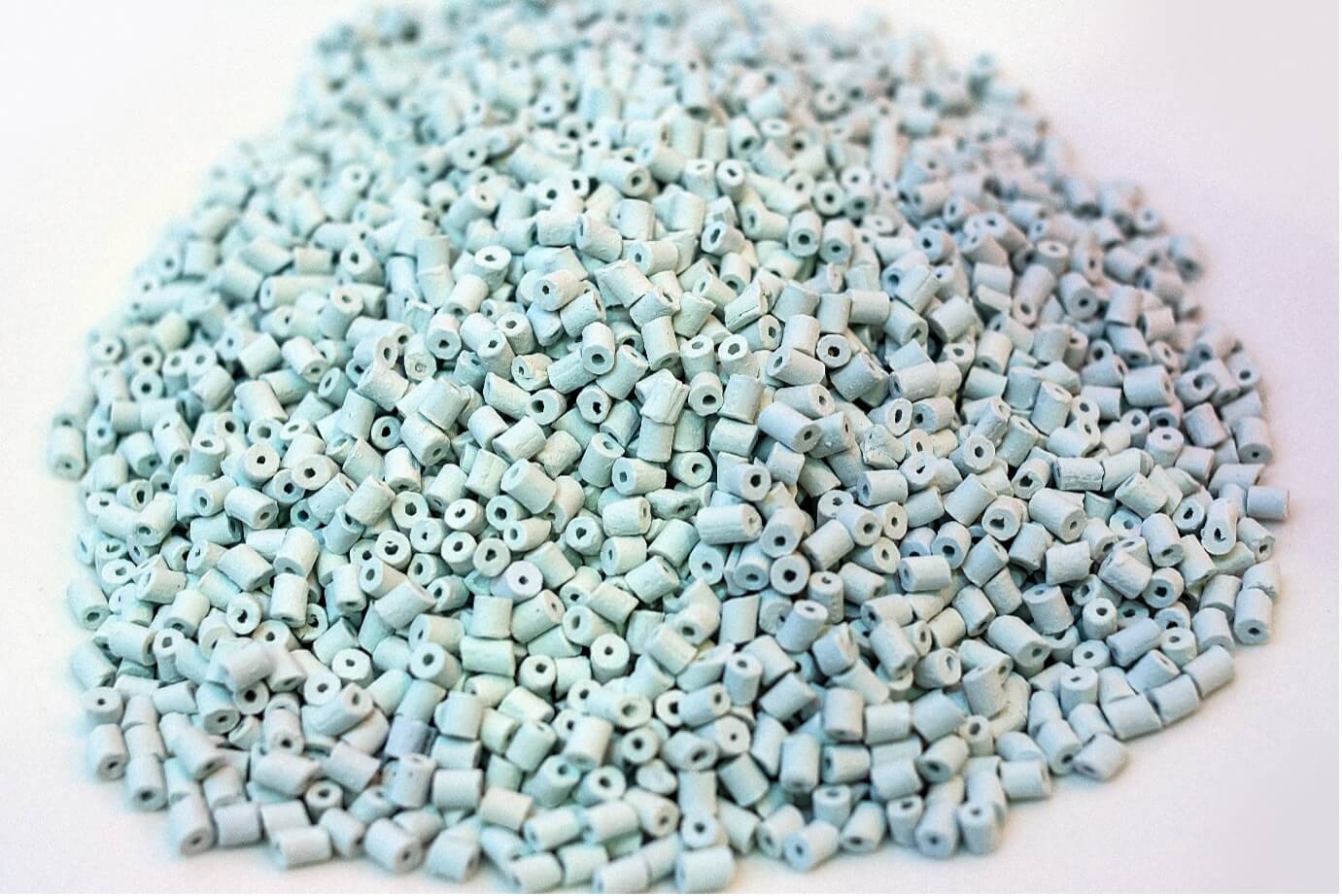
The catalytic ink in this study exhibited signs of over-dispersion. X-ray diffraction determined that the crystallite size of the nanocatalyst was larger in the ink and the deposited cathode layer than as-received powder. A common cause of such particle coarsening is overheating of the ink during dispersion. Additionally, laser diffraction detected a significant population of primary particles in the 20 nm size range, consistent with over-dispersion. Together, laser diffraction, X-ray diffraction, and dynamic light scattering are useful tools for optimizing and monitoring catalytic ink formulation and stabilization. Particle size analysis with the Mastersizer 3000 laser diffraction analyzer evaluates the effectiveness of critical particle dispersion. Zeta potential measurements with Zetasizer dynamic light scattering analyzer probes the interaction of the ionomer with the carbon-supported catalyst to predict ink stability. X-ray diffraction with the Aeris compact X-ray diffractometer measures the size of the nanocatalyst and the effectiveness of methods used to prevent nanoparticle coarsening.
Electrodes used in lithium-ion batteries have a defining influence on their electrochemical performance and are typically manufactured by coating a metal foil substrate with a multi-component slurry made of active electrode particles and conductive additives suspended in a binder solution. Size and shape distribution of electrode particles influences not only the rheology of this slurry in terms of its stability and ease of application, but also defines the quality parameters of the resulting coat like thickness uniformity, packing density and porosity. These, in turn, impact key battery performance parameters, such as ion transfer rate and battery recharge time.
The manufacturing of electrodes for lithium-ion batteries is a complex, multi-step process and presents a significant optimization challenge. Comprehensive analytical characterization with a range of complementary techniques provides a secure foundation for tackling this challenge, bringing value to both the individual components and the multi-component streams. All the techniques reviewed here have a place in the analytical toolkit for battery electrode manufacturers and all can play a vital role in meeting the targets of optimal production efficiency coupled with desirable electrochemical performance.
X-ray diffraction (XRD), laser diffraction (LD), and dynamic light scattering (DLS) are three characterization techniques with proven ability to scale-up in support of mass production. These three techniques each probe a different size regime and, when combined, can provide a comprehensive overview of the particles in the catalytic ink mixture.