Abstract: Isostatic pressing is a component-forming process where pressure is applied uniformly (using gas or liquid) to a hermetically sealed container filled with compacted metal powder. Isostatic pressing can be performed at elevated temperatures, known as hot isostatic pressing (HIP), or at ambient temperatures, known as cold isostatic pressing (CIP).
Isostatic pressing has several benefits over the commonly used press and sinter method, including equal compaction in all directions and a more uniform final component density. Nevertheless, as with other powder metallurgy processes, manufacturers must carefully characterize the metal powder’s properties for the process to be successful. Commonly characterized physical properties include powder flow, density, hardness, particle size, and particle shape of the respective powders.
Other key characteristics include chemistry and microstructure. Chemistry is paramount as the powder needs to comply with the alloy composition of the material specified, while phase composition and grain size can affect powder hardness and melt behavior which can affect the forming and sintering process.
X-ray diffraction is a powerful tool for material characterization as it provides information about the phase/mineralogical composition (ferrite, austenite, cementite, and other carbides) as well as crystallite size and microstrain in the sample powders. X-ray fluorescence provides accurate information about the elemental composition of the sample, and Automated Imaging can provide particle specific size and shape information.
>> Download the Application Note as a PDF
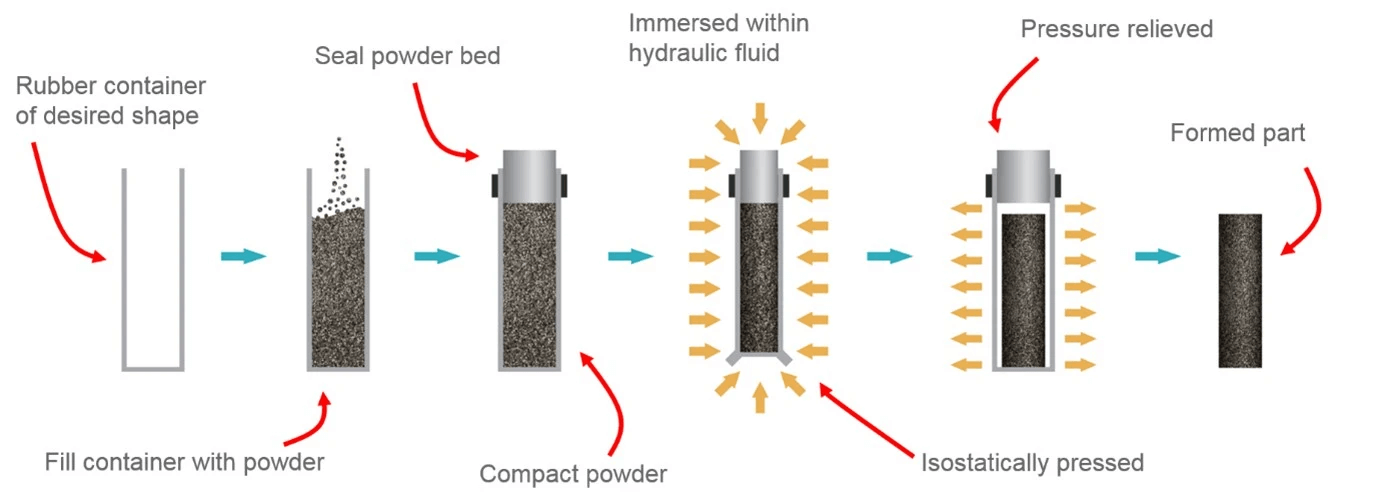