It is estimated that, in the UK alone, sales of formulated products amount to some £180 billion per year. From laundry detergents and personal care products to pharmaceuticals and food, formulation adds considerable value by conferring diverse and desirable performance characteristics. Historically, formulation has tended to rely on trial and error, giving it a reputation as something of a 'black art'. Today, the need to objectively evaluate performance, robustly verify quality, and substantiate product claims for increasingly complex formulations, calls for a more scientific approach. Rheology has an important role to play…
Trial and error... Formulators have two core strategies when it comes to manipulating the performance of a product: change the composition of the formulation; or change the physical characteristics of the ingredients by altering the conditions used for their manufacture. Consider the formulation of a creamy alcoholic liqueur, an appetizing example of an emulsion. To control the properties of the liqueur you could change the ingredients used or their relative proportions, the ratio of alcohol to cream, for example. Alternatively, you could alter the nature of the drink by changing the size of the emulsified droplets. This could be achieved by changing the processing conditions used to produce the drink - the operating pressure of the homogenizer used for emulsification. Understanding the impact of any changes made makes it easier to progress efficiently to a successful formulation. One approach is to directly assess how a change affects product performance – but this can be a lengthy process. In the case of the liqueur it might necessitate assessments of stability and/or mouth feel, for example, which could be both costly and time-consuming. … or the knowledge-led, re-engineering cycle If rheology is a part of the formulation toolkit then we have an alternative approach. Essentially rheology acts as a bridge – a reliable indicator of how changes to the formulation will impact product performance. Instead of making incremental changes to a formulation and empirically evaluating their effects on product performance, it becomes possible to identify and target rheological properties that will ensure success.
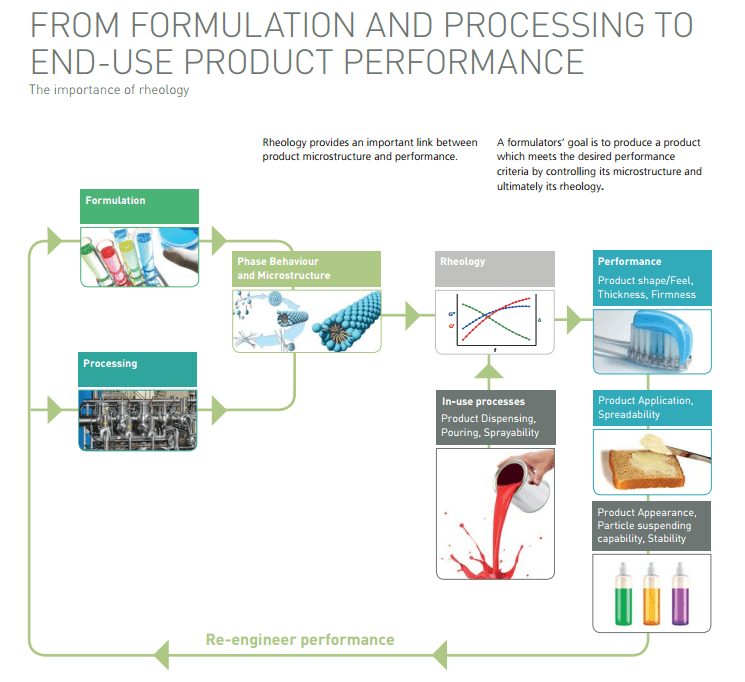
Rheology bridges the gap from formulation to end-use product performance, helping to accelerate formulation to a successful conclusion
The example of paint provides an easy to understand illustration of how formulation proceeds with rheology in place, as shown in the re-engineering cycle graphic above. An initial paint formulation is made. Measuring its rheology provides information about phase behavior and microstructure and, most importantly, an indication of how it will perform. For paint, for example, studies may reveal that efficient spray application requires a viscosity of less than 50mPas to be compatible with the spray head. So the target for the formulation process becomes not a relatively difficult to measure aspect of performance – easy of spraying and coverage – but a specific value of a defined rheological property. Changes can then be systematically made to the formulation to move it closer to this defined target in iterations of the re-engineering cycle. In the preceding discussion the viscosity target identified is the viscosity required under the high shear conditions that are applied by the spray gun. However, paints are usually suspensions making them susceptible to sedimentation. To prevent sedimentation it is beneficial for the paint to be relatively viscous under the low shear conditions that apply when the paint is sitting in a can, on a shelf. Furthermore, after application from the spray head the coating will be subject to these low shears also, with the corresponding viscosity impacting on the surface finish. Many of the complex fluids that form commercial products owe their success to non-Newtonian behavior. A non-Newtonian fluid has viscosity that varies depending on the stress that is applied to it, the ‘In-use process’ conditions (ref figure 1). To develop a secure correlation between rheological properties and product performance it is therefore essential to conduct rheological studies under relevant conditions. This raises the issue of how to choose the best rheological instrument for the job – but that's a whole new topic. In summary, adding a rheometer to the formulation toolkit gives insight into why changes to a formulation affect performance in the way that they do. This is valuable knowledge – and transferrable. Investing in a rheometer and learning to use it effectively can therefore be both productive and profitable. At the end of the day, trial and error experimentation may be engaging and interesting, but it is rarely either quick or cost-effective. 1 https://connect.innovateuk.org/web/formulation1
Malvern provides the materials and biophysical characterization technology and expertise that enables scientists and engineers to investigate, understand and control the properties of dispersed systems. These systems range from proteins and polymers in solution, particle and nanoparticle suspensions and emulsions, through to sprays and aerosols, industrial bulk powders and high concentration slurries. Used at all stages of research, development and manufacturing, Malvern’s instruments provide critical information that helps accelerate research and product development, enhance and maintain product quality and optimize process efficiency. Our products reflect Malvern’s drive to exploit the latest technological innovations. They are used by both industry and academia, in sectors ranging from pharmaceuticals and biopharmaceuticals to bulk chemicals, cement, plastics and polymers, energy and the environment. Malvern systems are used to measure particle size, particle shape, zeta potential, protein charge, molecular weight, mass, size and conformation, rheological properties and for chemical identification, advancing the understanding of dispersed systems across many different industries and applications. www.malvern.com Material relationships http://www.malvern.com/en/
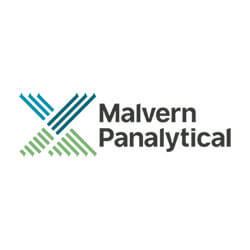