With Peter Kootstra’s background in medical and analytical chemistry, laboratories can no longer have secrets. After more than 25 years working for the government, Peter is now a consultant on analytical chemistry and quality assurance. He is co-owner of Lab-QAcademy, a provider of training courses and workshops on the quality assurance in laboratories. Peter believes that, by following a practical approach, the quality of laboratories can be improved: “If analyst know why rules are necessary, quality will be improved”.
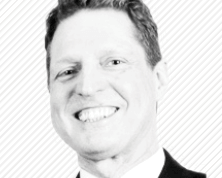
The Editorial in last month’s issue of this magazine dealt with the single most important topic for us as individual laboratory scientists and as a field devoted to analytics, namely, quality. As the Ford Motor Company slogan from the 1980’s put it, “Quality is Job 1”. Frank Van Geel’s critique did not focus on the word, but quality is at the heart of his concerns.
When you ask analytical scientists what they think about quality, they always respond that it is very important. So far, so good. But they invariably continue by stating that, in their company or institute, quality implementation is very bureaucratic and that they are fortunate that there is a dedicated quality manager. If you ask how many pages their Standard Operating Procedures (SOPs) run to, a typical response is around 20. And instead of using it, they have a scrap of paper in their pocket with about five lines of instructions; either they follow this note or they do it by heart, having done it so many times before. That is not a recipe for quality. Why are SOPs so long that nobody ever bothers to read them? The simple answer is division of responsibility. It’s the quality manager’s job to create and perpetuate the system, and the analyst’s job to get on with their task without paying any heed to ISO/IEC 17025 (the general requirements for the competence of testing and calibration laboratories), ISO 15189 (requirements for quality and competence of medical laboratories) or any other International Standard. And since only the quality manager has read the International Standard, it is his or her non-expert interpretation of the clauses that is followed. In all likelihood, the quality manual has been copied from another similar laboratory or bought over the Internet with the name of the new laboratory pasted into the original file. Some companies take the approach of hiring a quality consultant to help put the manual together. This seems like a good move on the face of it, but with no affinity to the organization or its needs, quality implementation is destined to turn out in a similar, substandard, way. Interpretation of the clauses of International Standards is difficult. Consequently, the standard written procedures will contain a lot of controls – the quality manager and the consultant will naturally think it better to be on the safe side. The result? Those long, bureaucratic procedures that the lab staff don’t see the need for, and a quality manual that spends its life on the shelf while the analysts refer to their ‘cheat sheets’. In this process, the quality manager performs most of the internal audits to check whether the staff members are following the written rules. It’s in everyone’s interest to fudge this, so that the entire organization convinces itself that (a) for quality there is a quality manager and (b) that he or she is implementing a quality management system.
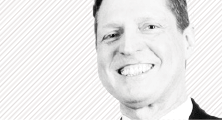
In fact, none of the standards encourage you to set up such a bureaucratic system. To build a genuine quality management system, the whole laboratory needs a thorough knowledge of the ISO standard. This does not start with the quality manager but top management; and it doesn’t end with the quality manager, but with the most junior member of the lab staff. Analysts must understand that producing results in a transparent and traceable way will help them to improve their methods and will reduce their workload. The quality system must be an integral part of the work, not a bolt-on. If you are in the analytical business, you owe it to yourself, your colleagues, your customers – and your quality manager – to implement the best system. And remember, it is never too late to improve.