Introduction
Many labs are facing helium supply difficulties and rapid price increases as a result of the helium shortage. Lab managers are therefore looking for alternative carrier gases and for many GC applications, hydrogen provides an excellent alternative to helium. Using a hydrogen generator can supply gas to a whole lab and at the same time remove the danger of storing hydrogen in the lab. Laboratories that switch gas supply from helium to hydrogen can see a number of benefits including reduced overheads, faster throughput and even improved separations.
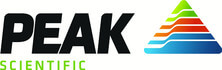
Carrier gases
Nitrogen, hydrogen and helium have differing relative carrier efficiencies along a velocity gradient (figure 1). Nitrogen offers good carrier efficiency at low velocities, but at high velocities, loses carrier efficiency. For this reason, nitrogen is not usually favoured for applications where helium or hydrogen can be used. Hydrogen offers very good efficiency at medium linear velocities and outperforms helium, in terms of carrier efficiency at very high velocities. In a response to growing demand for hydrogen for carrier gas, GC manufacturers have recently produced a number of systems or instruments that improve efficiency of helium use or allow a switch to hydrogen for carrier gas. Agilent have developed an EPC device for the GC-7890B which switches carrier gas from helium to nitrogen carrier gas when the system is idle. Agilent, Bruker and Shimadzu have all developed GC/MS systems that require no hardware changes in order to use hydrogen or helium carrier gas and Thermo have tested all of their GC systems for hydrogen carrier gas compatibility. Hydrogen is already used as a flame gas for FID detectors, one of the most commonly used GC detectors, however, the perceived health and safety risk of hydrogen means that many laboratories are now prohibited from having hydrogen cylinders in the laboratory. The safety concerns regarding placement of hydrogen cylinders in the laboratory stems from the large volume they contain (a 50 litre cylinder contains around 10,000 litres of pressurised hydrogen) and the dangers associated with moving heavy cylinders around. The high volume of hydrogen present in cylinders is a potential danger since a volume of 4% hydrogen in air equals the minimum threshold (lower explosion limit) for hydrogen ignition1. Hydrogen can also undergo auto-ignition if it is rapidly released into air2.
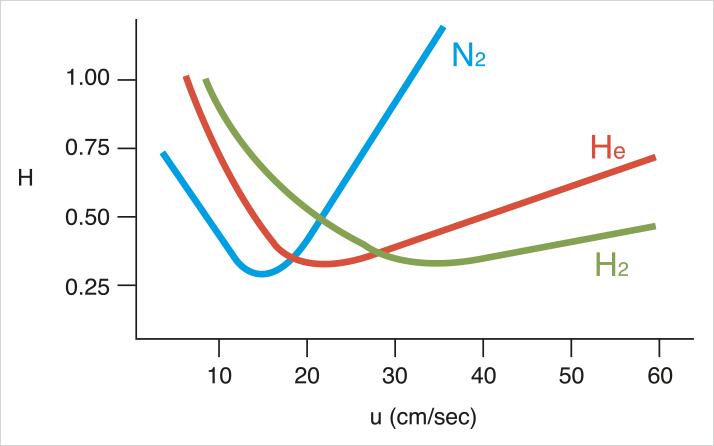
Possibly the biggest problem facing users of hydrogen cylinders is cylinder to cylinder variation in hydrogen quality. Changing empty cylinders can interrupt GC operation, introduce contaminants into the system as well as inconveniencing the user. Cylinders are also large and can take up a considerable amount of lab space. Gas generators, on the other hand have a relatively small footprint, contain a very low volume of hydrogen at any one time (less than 1000cc) and are able to produce gas on-demand to simultaneously supply carrier and flame gas to a number of GCs. The purity of gas produced by a hydrogen generator is often of higher purity than cylinder hydrogen. In addition to these features, hydrogen generators typically have forced air ventilation to prevent mixing of hydrogen and oxygen within the generator and an alarm system in case of low or high pressure. These features along with in-oven leak detectors supplied by hydrogen generator suppliers and emergency inlet shut-down features of GCs mean that laboratories should be quickly alerted in the event of a hydrogen leak.