Metal Injection Molding (MIM) is a growing industry. The size and shape of metal powders play a vital role in determining the process efficiency and properties of the final MIM components. Here, we look at image analysis as a tool for characterizing the size and shape distributions of atomized metal powders.
Introduction
The manufacture of complex shaped metal parts by Metal Injection Molding (MIM) is a growing industry. The shape and size of metal powders play an important role in determining process efficiency and properties of the final MIM components. Spherical powder particles are typically favored by MIM manufacturers looking to achieve best tolerances and properties in final components. Therefore, it is important to monitor atomized powder to ensure that particles of the desired shape and size are produced.
The metal injection molding process (MIM) is used in the manufacture of complexshaped, high volume, low weight parts where intricate detail may be required along with accurate tolerance control. It involves 4 crucial steps which are outlined below:
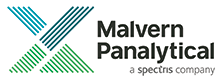
- Atomization of molten metal to form metal powders which are further processed by sieving and/or gas classification to obtain the appropriate particle size distribution. The powder is then mixed with thermoplastic binders to form pellets of feedstock ready for the next step.
- Feedstock is injected into a mold or die to form ‘green’ metal injection molded parts.
- The binder is removed from the ‘green’ part by solvent and/or thermal processes to leave a ‘brown’ metal part.
- The ‘brown’ part undergoes a sintering process in a high temperature furnace where the metal particles fuse together. Particle size is important during this stage, but so is particle shape since spherical powders will have a higher packing density. This means more touching surfaces, faster sintering times and reduced shrinkage resulting in better dimensional control. Therefore, the size and the shape of the original metal particles produced in step 1 will affect the final product and must be carefully controlled.