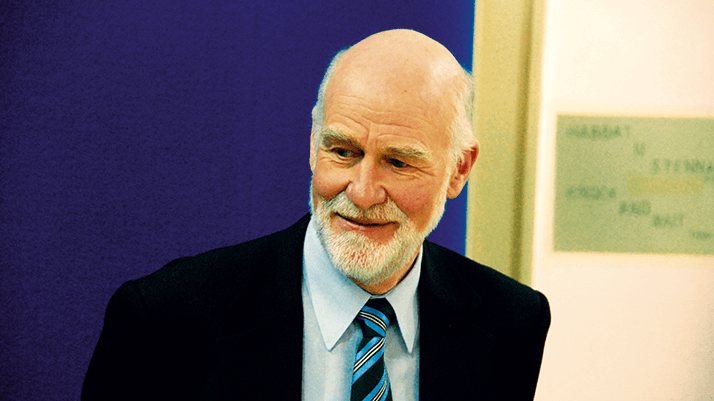
Today, a food contact material is, by definition, one that is approved for food applications – the EU, for example, has a positive list of starting materials and plastics additives restricted to substances that are deemed safe for food packaging. Polyolefins (HDPE, LDPE and PP), PET and polystyrene are probably the most important plastics in common use in bottle, sheet and film formats. Films can be particularly complex in construction, involving multiple laminate layers to achieve the desired properties, sometimes with adhesive between layers, and printing on the outer surface. Coated paperboard is also widely used; for example, in drinks cartons. Although polymers are generally inert, high-molecular weight, cross-linked substances that don’t migrate – the residual monomers used to prepare them can, and since it’s not possible to get a complete conversion to the polymer, oligomers may remain. Moreover, as indicated above, plastics need numerous additives to make them suitable for packaging – antioxidants, heat stabilizers, UV absorbers, plasticizers and colorants, and so on – there are literally hundreds of potential substances, which represents a significant analytical challenge. It’s fair to say that food-packaging analysis is very niche compared with, for example, pesticide residues, but there is a lot of awareness within the packaging industry – and the food industry certainly realizes it must comply with regulations.
Analytical drivers
Over the years, a great deal of food packaging regulation has actually been driven by developments in analytical techniques. Going back to the 1970s, MS and GC-MS were around, but the techniques were relatively specialized. People were using headspace GC with FID, and LC-MS was yet to be developed. As instrumental techniques have become more sensitive – and as costs have come down – methods have been developed and regulations established using the techniques available. Indeed, today’s regulations were beyond the realms of possibility back in the 1970s because the technology simply wasn’t available. Substances of below 1000 daltons in molecular weight are of particular interest, but can vary from simple volatile chemicals like vinyl chloride, acrylonitrile, vinylidene chloride through to complex mixtures of substances of much higher molecular weights like mineral oils. Migrants range in polarity from highly polar to non-polar organic molecules through to classical metals, as well as metal nanoparticles. Therefore, the full range of analytical tools must be employed in migration testing, including headspace GC-MS for volatiles, LC-MS/MS, LC-high-resolution accurate mass (HRAM) MS (Orbitrap) through to AAS and ICP-MS. Even DART-Orbitrap MS has been investigated for direct analysis of both plastics materials as well as extracts from plastics without any clean up.NIAS work
In 2011, Commission Regulation (EU) No. 10/2011 brought together numerous previous regulations, and introduced the concept of non-intentionally added substances (NIAS). The new regulations place responsibility on food producers to demonstrate due diligence for untargeted substances – a challenging feat. With NIAS, the substance could be a decomposition product from additives used in the plastic packaging or an adventitious contaminant – there is a huge range of possibilities. And that has led to a real interest in non-targeted analysis using LC-HRAM (Orbitrap-based) systems, where the ability to gain full-scan data at accurate mass is extremely useful. Right now, NIAS regulations are very general; they simply state that not only are you responsible for showing compliance to the positive list of substances, you also have to prove you have considered other potential contaminants, which by NIAS definition are unknown. It’s very typical in the regulatory world to begin with an indication of intention and then firm up on the detail of compliance later on. In time, someone might suggest an approach for providing assurance, and someone else will suggest it is validated. If CEN adopts it, it will become a definitive CEN standard for NIAS measurement. But, of course, these things take time... Right now, I would say that the industry is largely self-policing – especially given that food control or public analysts have limited resources. But that doesn’t mean it isn’t being proactive. The big worry for the food industry is a sudden scare and the resultant damage in reputation – and there have been several related to packaging. Photoinitiators represent a recent scare – especially as they decompose into free radicals when exposed to sunlight. Bisphenol A is also on the list, as it can migrate into food from the epoxy resin coating on the can or from polycarbonate food containers in certain circumstances. I believe that in due course, contract labs will offer comprehensive analysis using HRAM mass spectrometry for migrating substances from food packaging, just as they do for other residues and contaminants.The future of food contact materials
Packaging never stands still; innovation is continual. Take nanotechnology – the industry is looking for ways to improve the performance of packaging with nanoclays and other materials, such as nano-silver. There’s also a great deal going on in active packaging, where examples include ‘moisture absorbers’ used in meat trays, ‘scavengers’ found in small sachets used to absorb residual ethylene or oxygen, or ‘releasing systems’ that slowly release antimicrobial agents to extend shelf-life. There is also interest in whether it’s possible to incorporate antimicrobial substances into the packaging itself. Clearly, the food cannot be contaminated in the process. Indeed, all of these innovations represent new analytical challenges. And with nanomaterials, unlike other contaminants, it is not simply a case of measuring compound concentrations – particle size and particle size distribution are also important. There’s a good paper that uses Thermo Scientific ICP-MS to look at the migration of silver nanoparticles incorporated into plastic chopping boards into chicken meat (1). The regulators have to balance food safety (from a contaminant point of view) on one hand, but on the other, limit controls that get in the way of packaging innovations that are advantageous to the producer, retailer and consumer. Indeed, it is all too easy to think negatively about packaging when you consider substance migration and contaminants. But the reality is that packaging has made a huge difference to the food chain in terms of extending shelf life and availability; we no longer have to rely on locally available food products, and I would say the advantages far outweigh the disadvantages – it’s just a question of striking the right balance and using the right analytical tools and techniques to ensure safety. In my opinion, the push for sensitivity has largely ended (which was getting a little ridiculous in terms of identifying miniscule amounts of anything and everything). I believe specificity is also adequate – as long as the analysis is performed properly. What the food and packaging industries want is the ability to cover more analytes, at lower cost – and with greater speed. And as attention turns increasingly to non-intentionally added substances, we’ll see a concomitant growth in untargeted analyses.To watch John Gilbert’s comprehensive webinar on: “Analytical challenges in measuring migration from food contact materials” – register here
Related Content
References
- R J B Peters et al., “Development and validation of single particle ICP-MS for sizing and quantitative determination of nano-silver in chicken meat”, J Anal Bioanal Chem 406 (16), 3875–3885 (2014).