Back in the early 1970s (after gaining my PhD at Canterbury University here in Christchurch, New Zealand) I set off for a post-doctoral position at the Center for Research into Experimental Space Science at York University in Toronto, Canada. My goal? To study the ion–molecule reactions that were attracting such a lot of interest at the time.
Stellar beginnings
In the late 1960s, the advent of the smaller quadrupole mass spectrometer meant that it could be loaded onto a rocket; the US promptly did just that, and as it returned to Earth from the ionosphere, they began recording ions in the atmosphere. The results were unexpected in that different ions were observed than anticipated. A laboratory was established at the National Bureau of Standards in Boulder, Colorado, to investigate ion–molecule reactions and to explain how the ions in the atmosphere were interacting with atmospheric gases.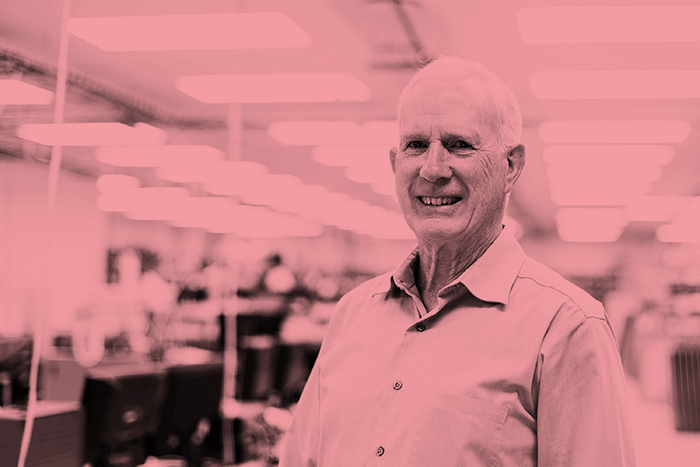

At almost at the same time, radio astronomy was coming into its own. Optical telescopes couldn’t tell us much about so-called interstellar clouds because they were opaque, but radio telescopes could look into their interiors. And they found that molecules existed there – another puzzle. There is very little material inside an interstellar cloud. On earth you might get 1019 molecules per cm3, while interstellar clouds contain a maximum of 106 molecules per cm3. They are also very cold – around 10 degrees above absolute zero. At that temperature, all chemistry stops, so how were the molecules being formed? Scientists soon began to speculate that ion–molecule reactions were behind the unusual results. Ion–molecule reactions are very fast and most have no activation energy – very different to neutral–neutral chemistry. The lab at York University was one of only a few around the world beginning to investigate ion–molecule chemistry. The very first reaction I studied was one of the most important in interstellar clouds – that between H3+ and CO. When I returned to the University of Canterbury, I continued to work on ion–molecule reactions. Whether we were studying atmospheric or interstellar chemistry, we were all asking the same questions: how does an ion react with a molecule and what are the products? The instruments we used to get the answer were large and cumbersome, with huge vacuum pumps and reaction tubes where the chemistry took place, and a quadrupole mass spectrometer to detect the ions formed. Initially, we used the flowing-afterglow technique: we flowed helium through large reaction tubes at low pressure, generating the ions at the upstream end of the tube, which were carried along by the helium to react with neutral molecules added at the downstream end. We would add our ions to the stream of helium gas in the flow tube, and study the resulting reaction. Later, we adopted the selected-ion flow tube (SIFT) technique – generating ions in a separate vacuum chamber and running them through a mass spectrometer to ensure that only the chosen ions made it into the reaction tube. To measure the speed of the reaction, we measured the concentration of the reactant and used it to determine the rate constant. Between the 1970s and 1990s, thousands of ion–molecule reactions had their rates and products determined in such a manner.
Flipping the concept
But in the mid-1990s, there was an important development. By now, a large database of ion–molecule reactions had been established. In 1996, two colleagues in the UK – David Smith and Patrick Španel at Keele University – decided to make use of that information to do something different. If we can measure the concentration over time to work out the rate constant, they reasoned, why not use the rate constant to determine the concentration of analytes in a sample? We thought this was a great idea and soon adopted the concept, using a microwave discharge of moist air to generate three main reagent ions – H3O+, NO+ and O2+ – to react with the analytes, and using mass spectrometry (MS) to detect the “product ions”. It was immediately clear that there was commercial potential for this work. The fast rate constants of ion molecule chemistry enable us to determine very low concentrations of analytes in air, and do it in just a few seconds; conventional techniques, such as GC-MS, take much longer and require highly skilled operators. To demonstrate the technology to visitors to our lab at Canterbury University, we would analyze their breath metabolites on the spot. On another memorable occasion, we had a visit from a researcher who had been working in the Antarctic, taking blood samples from seals. Her group was trying to determine how much fish the seals ate – with a simple headspace analysis of the blood samples we could measure the trimethylamine metabolites (essentially measuring how “fishy” the blood smelt), and so answer their question.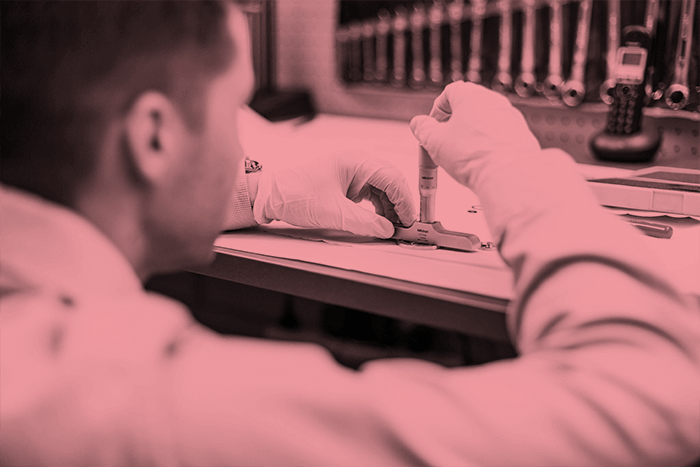
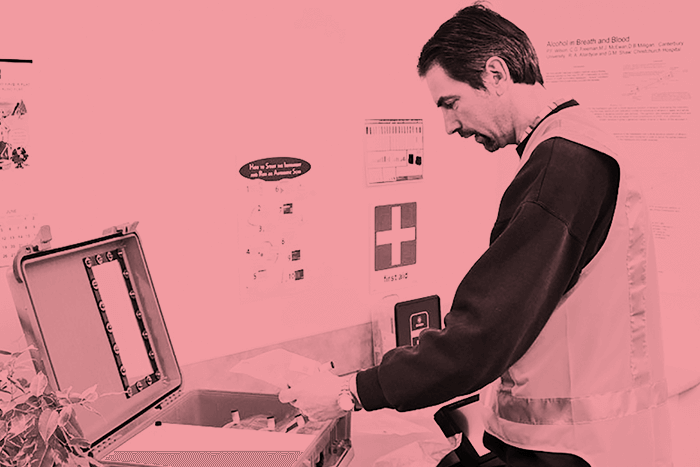
Ready for lift off
In the early 2000s, the university felt the time had come to commercialize the technology and, along with private investors, set up Syft Technologies Ltd at the end of 2002. The first thing we needed was a great team. We have found over the years that our very best students often take up positions overseas after graduating; Syft was an opportunity to get them back to New Zealand. New Zealand scientists returned from the US, Europe and Australia to work with us, and immediately set to work on making the technology commercially viable. Given that our laboratory instrument was over 5 meters long, weighed several tons and required a number of highly trained operators, the task was not a small one. Our ultimate goal was to create a device that could be operated even by completely untrained staff. The first instrument was the Voice 100, released in 2004. At 500 kg and around waist height, it did everything that the lab instrument did, was simple to use, and gave immediate results. Right after the Voice100, was released, we had an opportunity to prove the worth of the technology in the real world. Several shipyard workers in ports around the world had tragically died after entering shipping containers contaminated by toxic chemicals used for fumigation. The Australian government were having trouble monitoring these fumigants to ensure safe working conditions. They had been using colorimetric tubes that change color when fumigants are present, but they have a very high consumable cost, and workers found them too subjective. When they evaluated GC-based devices for frontline use they found that they couldn’t analyze all of the fumigants in question with a single chromatographic column; they had to use three. They heard about the capabilities of SIFT-MS and became our first customers, followed by the Canadian government and a number of major European ports. Whereas GC-MS typically needs trained operators, our instruments could be operated by staff working on wharfs, with virtually no scientific knowledge. The instrument is push-button operated, and the results are displayed on-screen as easy-to-understand concentrations, with an alert to flag dangerous levels of fumigants. It was a huge boost for a young company, and defined ease of use as a major selling point for SIFT-MS. The Voice100 was still rather unwieldy though, so we set about creating the next iteration – the Voice200, which was released in 2007. Not just smaller, the new instrument was also significantly more sensitive, and has since been further updated externally and internally. Until recently, there were some notable analytes that we couldn’t measure by SIFT-MS. For example, one of the fumigants that is used in shipping containers is vikane (sulfuryl fluoride; SO2F2). This molecule doesn’t react with any of our positive reagent ions, so we couldn’t measure it using our traditional approach. Another example is hydrogen chloride gas (HCl), an important contaminant in the electronics industry. Around 18 months ago, we made a change in the way we operate our ion source, allowing it to generate negative ions – O-, OH-, O2-, NO2- and NO3-. Those ions react with many of the molecules we weren’t previously able to measure, filling an important gap.Dark days
When the company was set up in 2002, I was a university professor and had precisely zero experience of start-ups. It’s fair to say it’s been a steep learning curve. Initially, we thought that we could stay in New Zealand because the power of the technology would be enough to bring people to us. But of course, people had never heard of us. Chromatography has a long pedigree – it’s well-established and people understand it. To move to a completely different technique is a real leap, and we faced a lot of skepticism. We were making heavy losses, and questioned whether we could survive. Things looked grim. Fortunately, some of our investors stood by us, saying, “We believe in this technology.” Seeing our instruments being used by customers in wonderful ways – especially some of the exciting clinical diagnostic applications that were emerging – kept us going. In 2009, some of the major shareholders invested in the company to keep it afloat. In 2012, we gained a new CEO (Doug Hastie) and management team, who brought a new approach to sales, and the company has gone from strength to strength ever since.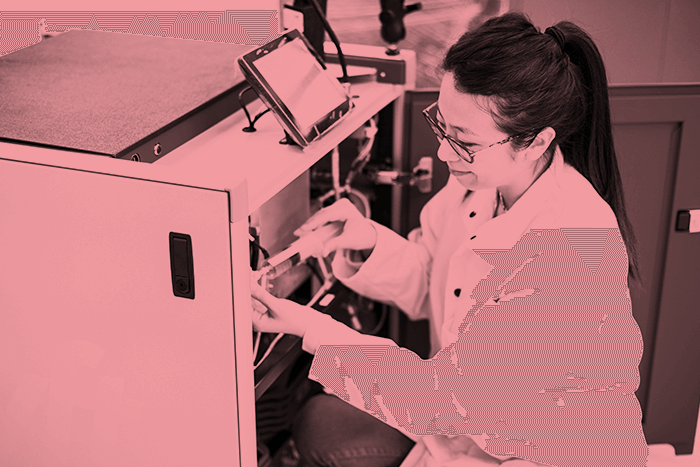
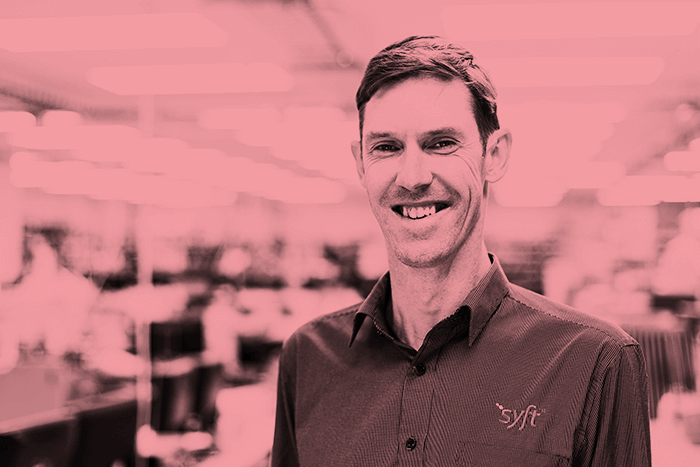
We now have agents all over the world selling our instruments – partners with greater visibility than we could hope to achieve. Agents like Anatune, who are experts in GC-MS, were able to talk knowledgeably to their customers about the deficiencies of GC-MS and why SIFT-MS is an attractive alternative. We get many repeat customers; Samsung now have more than 20 of our instruments. At one point we were down to 17 employees. We now have over 45 permanent staff, plus around 30 students over the southern-hemisphere summer vacation – all working hard to further develop the technology. Their talent, enthusiasm and commitment are the biggest thing we have going for us, and we’re proud to think that we’re bringing talented scientists back into New Zealand who might otherwise be working overseas.
What’s next?
People are beginning to recognize the opportunities that rapid monitoring of volatiles opens up, and our customers are finding all sorts of uses for SIFT-MS, some of which we had never even dreamed of (see “From Garlic Breath to Clean Rooms”). As we become better known – and as customers approach us with exciting new applications – there are a lot of conversations to be had (and significant air miles for our staff!). We are exploring the potential for automating the technology, along with our UK partners Anatune Ltd, which we believe will open up new opportunities in the pharma industry. Murray McEwan is Chief Technical Officer at Syft Technologies Ltd, and Professor Emeritus at the University of Canterbury, Christchurch, New Zealand.SIFT-MS isn’t a universal replacement for chromatography, but when customers need to do things faster – or analyze compounds that don’t lend themselves to existing techniques – SIFT-MS can have a real impact.
By Vaughan Langford Protecting workers As noted by Murray, our very first customers were port authorities, who used SIFT-MS to detect toxic fumigants in shipping containers. The technology is now being applied in manufacturing settings too; for example, in clean rooms where semiconductors are manufactured. As semiconductors have become more sophisticated, it’s become crucial to ensure that VOCs and other gases are kept to a minimum in the clean room. Gases can impact on the quality of the semiconductor films that are being laid down, so companies are increasingly adopting continuous low-level monitoring. In the past, if they monitored VOCs at all, companies used thermal desorption GC-MS and a multi-port sampling system – using a single instrument and cycling through different work areas, typically measuring two points per day per site. SIFT-MS allows you to monitor continuously, pick up problems faster and so save money through avoiding loss of product. Another fast-growing application is vehicle interior air quality. Around 20 million cars are made in China every year. The plastics used inside the vehicles produce volatile chemicals, some of which have been shown to be harmful (the coveted “new car” smell may have a sting in the tail). Governments are now starting to pass legislation to limit the concentration of some of these chemicals. Legislating is one thing, but how do you measure it? Prior to SIFT-MS, companies were reliant on GC-MS and other off-line techniques, which are difficult, time consuming and expensive (up to US$1,500 per car). SIFT-MS is also well adapted to environmental monitoring, and Samsung use our instruments to monitor a range of pollutants and odor compounds at the boundary of their semiconductor factories in South Korea. The smell of success Odor analysis is another application area where I believe SIFT-MS can have a significant impact as it gains wider acceptance. In 2008, two professors at Ohio State University – Jim Harper and Sheryl Barringer – starting using one of our instruments for their studies into food odors. Barringer has since published more than 30 academic papers using the technology for a whole range of different food products, probably the most significant of which has been on garlic malodor on breath. Using SIFT-MS, Barringer was able to show that eating apple, mint or lettuce can help neutralize volatiles responsible for “garlic breath” – including diallyl disulfide, allyl mercaptan, allyl methyl disulfide, and allyl methyl sulfide – a finding that gained her a great deal of attention in the press (1). Our instruments have also been used at the University of Ghent for a number of applications, including determining fish freshness. Odor compounds are notoriously difficult to analyze by chromatography. The best detectors are human noses, but odor panels are expensive, human senses vary, and people get fatigued. SIFT-MS can detect the key compounds in a single analysis; from the odorous aldehydes, the volatile fatty acids, right through to organosulfur compounds, all of which require derivatization or other chemical pretreatment prior to chromatography. Various different analyses for chromatography can all be performed simply and quickly with one instrument, and that’s likely to be a big draw. The promise of breath analysis One of the reasons that Syft Technologies attracted investment was the hope of developing breath diagnostics. It’s tough to identify biomarkers in the low ppb, and breath analysis – whether by SIFT-MS or other means – has been slower to deliver results than many people had hoped. But we have several customers doing good work, and researchers recently reported promising results describing SIFT-MS analysis of several compounds that are diagnostic for esophageal and stomach cancers (2). Differences in levels of butyric, pentanoic and hexanoic acids, plus butanal and decanal, had an overall accuracy of 85 percent in identifying patients with stomach or esophageal cancers. Vaughan Langford is Director of Applications at Syft Technologies Ltd, Christchurch, New Zealand. References 1. R Mirondo, S Barringer, “Deodorization of garlic breath by foods, and the role of polyphenol oxidase and phenolic compounds”, J Food Sci, 81, C2425–C2430 (2016).2. NHS Choices, “Breath test shows potential for detecting cancer” (2017). Available at: http://bit.ly/2jx5G2c. Accessed 25 May 2017.