Drilling muds and drilling fluids are fundamental to the practice of oil extraction and particle size of the key constituents has a critical impact on how they perform in the field. The American Petroleum Industry (API) is currently working towards a standard for particle sizing in drilling muds that is based on the use of laser diffraction techniques. This article looks at the suitability of modern laser diffraction systems for the measurement of these industrially essential formulations and considers how their application contributes to both the efficacy of the drilling muds and fluids and the success of the drilling process. Drilling muds are complex aqueous or oil‑based suspensions that are designed to fulfil several important functions within drilling processes, ranging from lubrication and cooling of the drill string through to preventing invasion of rock fragments and liquids into a geological formation. Because of the variations resulting from different rock formations and drilling conditions, drilling muds must be tailored to meet the demands of specific applications. The need to respect what can be a relatively sensitive ecosystem adds to this challenge. In order to meet these challenges, formulators must control the drilling mud performance by manipulating the mud composition and the properties of the constituents. They may also use a range of polymeric and other additives to achieve the required behaviour.
A significant factor in the effectiveness of drilling muds is the properties of the particles within them, such as particle size and potentially particle shape as well. These affect the way in which a drilling mud interacts with the surrounding geology as well as influencing the rheological properties of the mud system. Particle size measurement is therefore one of the tools that formulators rely upon when creating high‑performance drilling muds that have low environmental impact. >> Download the full article for FREE
Malvern provides the materials and biophysical characterization technology and expertise that enables scientists and engineers to investigate, understand and control the properties of dispersed systems. These systems range from proteins and polymers in solution, particle and nanoparticle suspensions and emulsions, through to sprays and aerosols, industrial bulk powders and high concentration slurries. Used at all stages of research, development and manufacturing, Malvern’s instruments provide critical information that helps accelerate research and product development, enhance and maintain product quality and optimize process efficiency. Our products reflect Malvern’s drive to exploit the latest technological innovations. They are used by both industry and academia, in sectors ranging from pharmaceuticals and biopharmaceuticals to bulk chemicals, cement, plastics and polymers, energy and the environment. Malvern systems are used to measure particle size, particle shape, zeta potential, protein charge, molecular weight, mass, size and conformation, rheological properties and for chemical identification, advancing the understanding of dispersed systems across many different industries and applications. www.malvern.com Material relationships http://www.malvern.com/en/ [email protected]
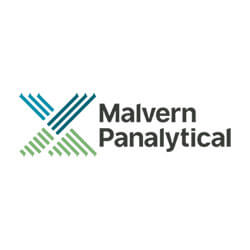