Controlling the performance of an ink is a complex optimization challenge. Understanding how features of the system, the dispersed particle size in particular, impact stability and behavior during each stage of the printing process is crucial for effective formulation. This white paper offers practical guidance on using a range of analytical techniques, including rheology, and particle size and zeta potential measurement, to generate the required knowledge. Over the past 30 years, the use of commercial and industrial inks has changed substantially. In particular, the maturation of inkjet technology has revolutionized printing. From office printers through to industrial coding and marking systems, inks are now required to meet demanding performance targets, for a wide range of different applications. Inks are complex dispersions or emulsions consisting of dyes or pigments, and other components, suspended within a continuous phase. Formulation is complicated by the fact that the properties of these components impact multiple aspects of ink performance. For example, the particle size of a suspended pigment determines the hue, gloss and weatherability of the finished coating. At the same time it also affects the stability of the ink and its flow properties (viscosity). Ink formulation is an exacting science and relies on gathering relevant data from multiple analytical techniques to achieve an optimal solution.
In this white paper, experts from Malvern Instruments explore analytical strategies that support formulation and provide practical guidance on gathering data to:
- characterize ink components
- quantify performance characteristics such as jetability and tendency to drip
- engineer formulation stability
- control manufacture.
- Case studies are presented to illustrate the value of different analytical techniques in accelerating formulation to a successful conclusion.
Innovations in inks
Every advance in printing requires an associated advance in ink formulation. The invention of the printing press, for instance, called for thick oil-based formulations to cling to the metal type face, in place of the high viscosity water-based inks that were prevalent at the time. Today, modern developers face the challenge of developing high performance inks that produce a consistently high quality finish, for every type of printing technology.
There is no universal ink formulation that will perform well in all types of printing process. For example, inks are required to flow more quickly through an inkjet printer head than when applied via screen-based techniques, so the preferred viscosity characteristics are different in each case. In addition, advances in technology have extended printing to a diversity of substrates, from thin films and vinyl sheets through to ceramic tiles and objects with three-dimensional features. For success, performance-defining characteristics of the ink must be engineered for compatibility with the printer and the substrate, as well as delivering a desirable finish.
Components of modern inks include:
- a carrier fluid – either aqueous or organic
- colorants – pigments or dyes
- surfactants – to control the surface tension of the ink droplets
- binders – to control the elasticity of the ink and the way in which it breaks up when shear is applied
- dispersants – to improve the dispersion of colorants in the carrier fluid.
The formulation of high performance, stable products relies on the optimal inclusion of each of these constituent components.
Controlling performance during the printing process
A good starting point for formulation is to consider the requirements of the printing process and how to make an ink compatible with these. Here, rheology has an important role to play, as rheological characteristics impact the way in which an ink jet atomizes, drips and spreads.
Figure 1 shows two inks being used in a ‘drop-on-demand’ inkjet printing process. The first behaves properly, producing a single discrete drop following actuation, while the second behaves improperly, producing double droplets. This disruptive dripping behavior is typical of inks with poorly optimized rheology and it compromises printing performance.
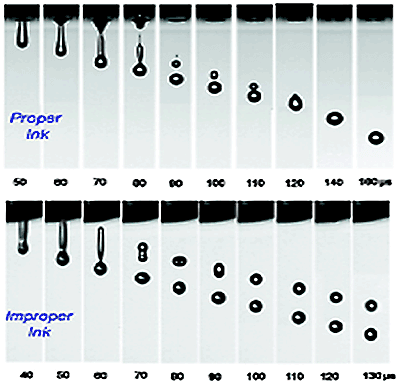
Figure 1: Comparison between a proper (top) and improper (bottom) ink within a ‘drop on demand’ print head illustrates the importance of controlling formulation rheology The rheology of an ink is directly influenced by properties of the suspended components, such as particle size. However, particle size specifications for a suspended pigment are often dictated by formulation goals relating to the finish. For any given carrier fluid/pigment combination, the rheology of the continuous phase is more practically manipulated through the use of polymers, surfactants and binders. Polymeric additives can be used to control the viscosity of the continuous phase, and to impart sophisticated characteristics such as elasticity or shear thinning behavior.
Viscosity
Simple viscosity measurements quantify how an ink will flow through the print head, and to some extent how it will atomize. Successfully incorporating additives designed to control viscosity requires an understanding of the structure-function relationship between additive characteristics, such as molecular weight and molecular weight distribution, and ink performance. Techniques such as multi-detector gel permeation chromatography/size exclusion chromatography (GPC/SEC) enable the detailed characterization of polymeric additives. Rheological measurements quantify viscosity and, by extension, ink performance. To be relevant and useful, viscosity values must be measured under conditions that simulate those at the print head. This can be challenging when designing for modern printers, which typically apply shear rates as high as105 to 106 s-1. These shear rates are not achievable with even the most highly specified rotational rheometers because of the inherent mechanical limitations of the technology. The following case study demonstrates how microfluidic rheometry, a relative new technique, more efficiently meets the need for high shear viscosity measurement. Case Study 1: Using microfluidic rheometry to assess performance at the print head1 Research suggests that for a ceramic inkjet ink a viscosity of between 5 and 25 mPa.s is optimal for good performance at the print head. Figure 2 shows viscosity measurements made to assess how the viscosity of two commercial ceramic inkjet inks vary as function of temperature, in the range 20°C and 40°C. This range reflects typical operating temperatures during printer use.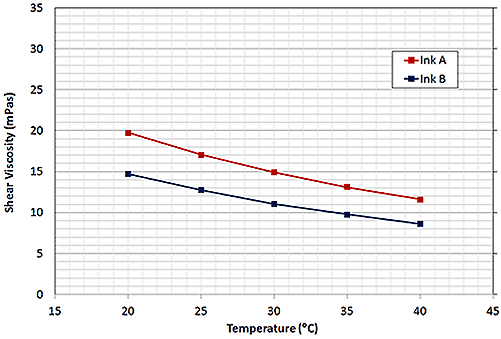
Figure 2: Measurements at high shear (30,000 s-1), made with a microfluidic rheometer, confirm that viscosity remains within the target range of 5 to 25 mPa.s across an operating temperature range of 20 to 40°C
The results show that the viscosity of both inks decreases with increasing temperature, as expected. However, the shear viscosity of both inks remains within the desirable range across the test temperature range. This suggests that both inks will flow well through the print head, under normal operating conditions.
Viscoelasticity
The rheological characteristic of viscoelasticity also directly influences performance at the print head. Suspensions exhibit behavior that lies along a spectrum ranging from viscous, liquid-like behavior to the elastic response to shear associated with solids. Measuring and controlling viscoelasticity supports the development an ink that successfully breaks up into discrete, well-defined droplets, during printing and holds its desired structure on application to the substrate. Referring back to the poor jetting performance illustrated in figure 1, this is indicative of an ink with sub-optimal viscoelasticity. The ability of the elongated droplet to break from the bulk liquid and re-form into a single sphere is linked directly to the property of viscoelasticity, and also to the surface tension of the ink.
Developing structure-performance relationships to enable the successful incorporation of additives to control viscoelasticity relies on quantifying this more complex aspect of rheological performance. Here rotational rheometry is a valued technique. However, because inks are so weakly structured, alternative strategies can be helpful. Microrheology is an emerging technique that is useful for probing viscoelasticity under conditions that give valuable insight into performance at the print head.
Engineering stability
Formulating for successful printing is crucial but it is equally important to look at how to maintain that performance over time. Engineering a robustly stable formulation ensures that ink quality does not degrade with time and relies on maintaining discrete particles in suspension, under the conditions encountered during use and in storage. This can be one of the most challenging aspects of ink formulation.
The general strategy for achieving stability is to avoid particle aggregation since this produces larger particles that are more prone to sedimentation or settling and can block the print head. In addition, the presence of aggregated particles in a finish can adversely affect quality. The mechanisms that give rise to stability can be classified as kinetic or thermodynamic. Kinetic stability is associated with particle movement. Slowing particles down induces kinetic stability by reducing the risk of aggregation and sedimentation. Achieving thermodynamic stability on the other hand, depends on discouraging aggregation by increasing the strength of repulsive forces between fine particles, usually through electrostatic or steric means. These forces
The likelihood of sedimentation in a suspension can be predicted from the ratio of gravitational to Brownian forces, see equation 12

[where a is the particle radius, Δρ is the density difference between the dispersed and continuous phases, g is acceleration due to gravity, kB is the Boltzmann constant and T is the temperature] In a sub-micron suspension Brownian motion is usually significant and this ratio has a value of less than 1. For these systems thermodynamic stabilization is usually required to prevent aggregation. A ratio in excess of 1 is indicative of a system prone to sedimentation as a result of gravity driven kinetic instability. When it comes to the practicalities of controlling the ink stability, formulators can manipulate one or more of the following three variables:
- Particle size of the dispersed phase. Larger particles are more prone to sedimentation than those that are finer. However, small dense particles, as exemplified by many pigments, will settle because of the large density difference between the dispersed and continuous phases (see equation 1).
- Viscosity of the continuous phase or the suspension. Increasing viscosity slows down particle movement and tends to decrease the risk of sedimentation.
- Zeta potential of the system. Zeta potential is a measure of the charge between particles at the slippage plane1. In systems containing sub-micron particles, a zeta potential with a magnitude of greater than 30 mV, either negative or positive, is associated with a high degree of repulsion between particles, and thermodynamic stability. Steric repulsion through the adsorption of macromolecules or surfactant provides an alternative route for stabilization particularly for non-aqueous systems.
Malvern provides the materials and biophysical characterization technology and expertise that enables scientists and engineers to investigate, understand and control the properties of dispersed systems. These systems range from proteins and polymers in solution, particle and nanoparticle suspensions and emulsions, through to sprays and aerosols, industrial bulk powders and high concentration slurries. Used at all stages of research, development and manufacturing, Malvern’s instruments provide critical information that helps accelerate research and product development, enhance and maintain product quality and optimize process efficiency. Our products reflect Malvern’s drive to exploit the latest technological innovations. They are used by both industry and academia, in sectors ranging from pharmaceuticals and biopharmaceuticals to bulk chemicals, cement, plastics and polymers, energy and the environment. Malvern systems are used to measure particle size, particle shape, zeta potential, protein charge, molecular weight, mass, size and conformation, rheological properties and for chemical identification, advancing the understanding of dispersed systems across many different industries and applications. www.malvern.com Material relationships http://www.malvern.com/en/ [email protected]
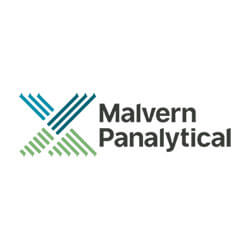