Shortages and supply chain disruptions have recently reduced the availability and increased the price of helium. Certainly, switching to hydrogen is a viable option for some applications, but sometimes that is not possible or desirable. How can we make more efficient use of helium in gas chromatography?
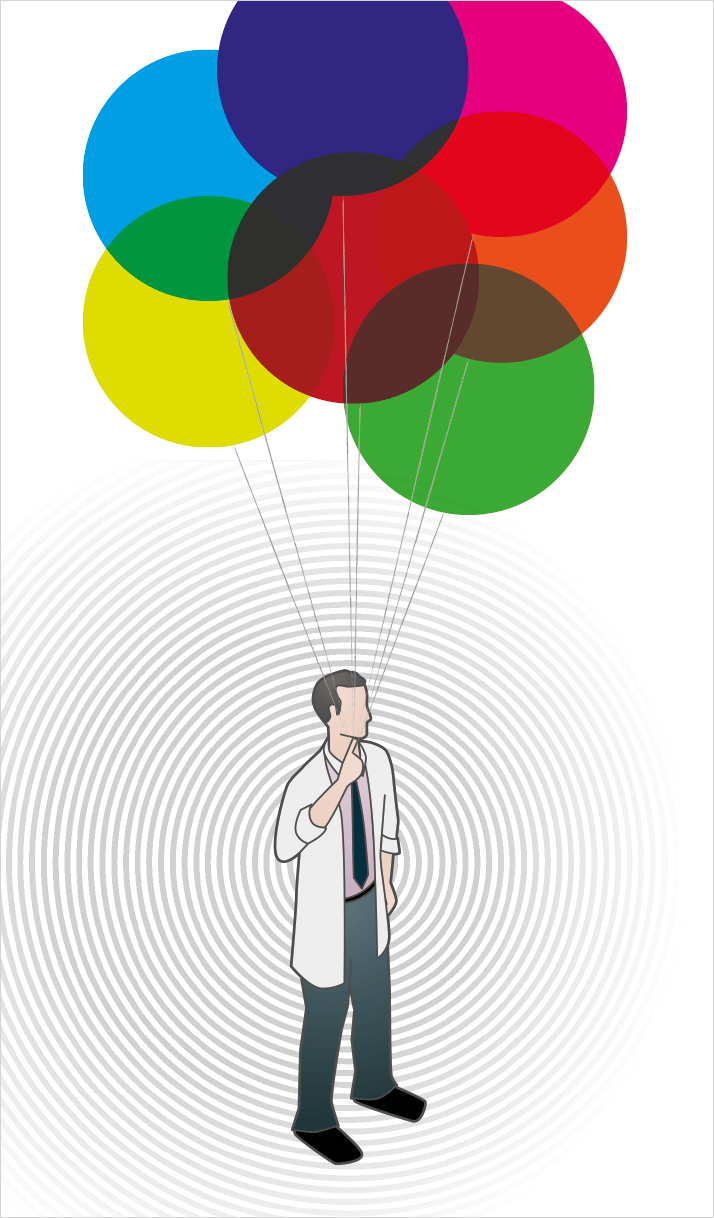
Back in my chemistry set days, I was fascinated with helium balloons, lighterthan- air craft, and things that went “boom”. I would spend hours collecting zinc from dead batteries and occasionally “borrow” a bit of muriatic acid from a neighbor’s pool house. Flaming dirigibles were only a bottle, a balloon, and a cigarette lighter away... Things have changed considerably since the ‘good ol’ days’, but the chemistry of helium and hydrogen has remained the same. One is remarkably inert, while the other is a bit more gregarious. Despite their differences, helium and hydrogen are the only viable carrier gases for GC-MS instrumentation today. In light of the recent helium shortage/ supply-chain disruptions, a lot of attention has focused on switching from helium to hydrogen as a carrier gas for GC-MS work. The advent of low-cost bench-top hydrogen generators makes this switch appear attractive. Such units can produce remarkably pure hydrogen and remove the need to deal with high pressure cylinders in the laboratory. For fast GC or in fields where methods are not highly regulated, hydrogen may be the best choice. Indeed, hydrogen systems can deliver GC peaks that are both faster and slimmer than those of their helium counterparts.
However, though hydrogen does indeed offer the ‘sexiest’ chromatography, it is not a panacea. This is particularly true when a mass spectrometer is on the receiving end. Hydrogen has poorer pumping speed, lower sensitivity in electron ionization (EI) by a factor of about three; forms a reactive plasma in the ion source that can alter spectra; requires changing standardized method retention times and response factors; can react with analytes or halogenated solvents in the hot zone (particularly with active sites)… and it has the potential to go “boom”. (In fairness, hydrogen generators can be safe, particularly when a hydrogen sensor is placed in the GC oven proper.) Traditional methods of reducing helium consumption include lowering the amount of gas that is split, switching to a standby gas, such as nitrogen, when the instrument is idle, or “simply” switching to a different carrier gas, such as hydrogen. Reducing the split flow can cause elevated baselines or premature fouling of the head of the column, since the outgassing of matrix residuals is not as effectively diluted. Switching to a standby gas when the instrument is idle is a solution, particularly if end users never intend to use their instrument. If they do, there is a protracted waiting period on start up due to nitrogen saturation of the carbon filter upstream of the split/splitless (SSL) injection port. There is a far superior way to conserve helium: decoupling the purging process from the analytical gas requirement.
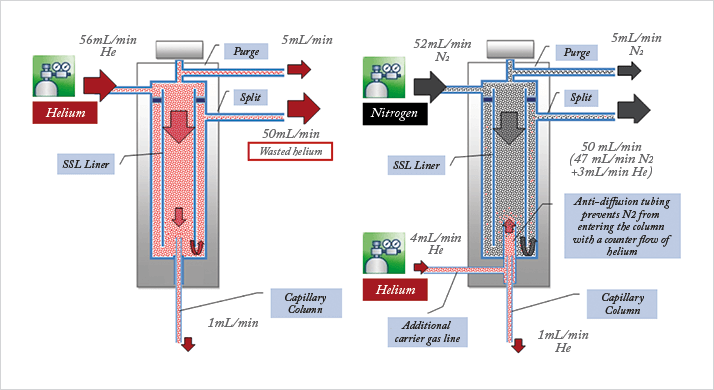
The value of decoupling the purging gas from the gas used during analysis is readily apparent in Figure 1,where helium is consumed in an SSL-type injector. About 1 ml/min is used for the analytical separation (column flow), 50 ml/min is used for the split flow, and 5 ml/min is used for the septum purge. (Mileage may vary). So, 55 times as much gas is used to purge matrix residuals from the liner, and silicone goo from the septum, than is used for the chromatographic process. I first became interested in the wasted gas at the split and septum purge vents in 2009 and devised a device that harvests the wasted gas, compresses and purifies it then re-introduces it into the supply stream. This solution was quite complicated. Even at the time, I thought there simply must be something more elegant. A few months later, I found myself on the telephone with Paolo Magni, a chromatography expert and colleague of mine in Milan, Italy. We were talking about oxygen diffusion through graphite ferrules using a split/splitless injector in backflush mode (who hasn’t had that conversation?). In this mode of operation, the entire injector flow is routed, during backflush, to a tee piece that is inserted between the analytical column and a large bore pre-column. One of the downsides of this arrangement was that since the total flow is imposed, the split flow setpoint affects the retention times due to the pressure drop of the pre-column.
I began to imagine what might happen if the flow were reduced to only a few milliliters per minute. The pressure would not drop, but could not be controlled with the same precision, and the purge flow would be very low and inefficient. So, why not use a secondary helium source, set to deliver only a few milliliters per minute at the tee through a tiny bore capillary with a high input pressure? If the pressure drop of the pre-column is indeed low, the electronic pressure control of the inlet could be used to effectively control the pressure at the tee junction and the small backflow of helium would simply contribute to the helium already in the inlet. The actual flow to the tee would not be critical, since only the pressure is important to provide the correct column flow. During this discussion with Paolo, it dawned on me that during backflush, a separate gas such as nitrogen, argon, or hydrogen could be used to purge the inlet and reduce helium consumption. As long as the backflow of helium was sufficient to occlude back-diffusion of the secondary gas, it would work. In fact, only a very short pre-column is needed to prevent back diffusion of the secondary gas. And this was the key to using this idea on an SSL without backflush. Rather than using a pre-column to cold trap and selectively backflush analytes at a specific oven temperature, a short heated pre-column could be used so that injected components would fully transfer to the analytical column, then “backflush” immediately following sample transfer. This modification would allow dramatic reductions in the consumption of helium if, say, nitrogen were used to pressurize the inlet.
Since the required “pre-column” is quite short, it is advantageous simply to incorporate it into the body of the injection port. This short back-diffusion barrier needs only be about a centimeter long to work with most capillary columns. Incorporation into the injection port allows the pre-column to be heated without a separate heating element. It also makes it possible to eliminate the separate tee piece in the oven. In practice, we used a short segment of hypodermic needle stock with an internal diameter just larger than the outer diameter of the column. The needle stock is stainless steel, which has been treated using a proprietary process to render the surface inert. The inert coating and short residence time ensures no interaction with injected analytes. Furthermore, matrix residuals resident in the glass liner are precluded from out gassing onto the head of the GC column, reducing the frequency of column trimmings to restore chromatography.
The hardware solution consists of a subcomponent SSL injector and a specially modified insert. The helium delivered to the back-diffusion barrier is controlled using a solenoid valve set to deliver a residual purge of approximately 0.1 mL/min (nitrogen acts to transfer the injected sample), or approximately 4mL/min during analysis. Flow is not critical, as long as it is above the amount necessary to occlude nitrogen. The excess helium is simply diverted upward, where it contributes to the bulk nitrogen purge. This helium-saving solution allows a cylinder of helium to last for 3.5 years with continuous use and up to 14 years, if put in standby mode overnight and on weekends. The standby condition consumes only 0.1 mL/min.
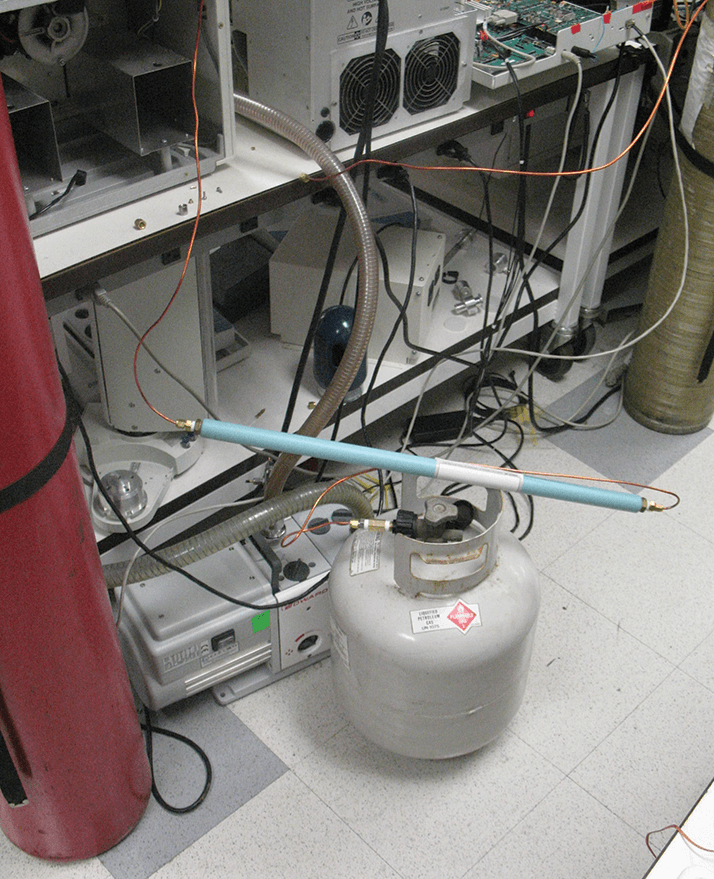
Decoupling the purge gas requirements from those of the analytical gas as described above, opens up several possibilities. While nitrogen is the gas of choice for the purge gas, it might also be possible to use argon, methane, propane, or carbon dioxide. Liquefiable gasses, in particular, offer high capacity for a given cylinder size. To prove a point, one day I attached a propane cylinder from my home barbeque grill (see photo). A regulator wasn’t even required. (Note: Please don’t try this. The olefins will eat your lunch. There are far too many impurities in fuel-grade propane!) Alternatively, air might be used as the purge gas. The oxygen in air can cause column and sample degradation, but it is possible to plumb the pneumatics with a three-way valve such that helium is used for the short duration of the injection. This way, the column and sample are never exposed to oxygen.
Another example of going ‘beyond the solution’ is direct coupling of a purge and trap concentrator. Instead of using helium to desorb the trap and act as carrier, one can simply use nitrogen for purging and desorbing, compounding helium savings. And for hard-core hydrogen users, the technology may reduce the potential for halogenated solvents or unsaturated analytes to react with hydrogen in the hot inlet. Nitrogen would be present during the injection, but then hydrogen would be used for the chromatography. Since the hydrogen is restricted to only a few mL/min, there would be far fewer safety concerns. Generally, a column break near the injector results in high hydrogen flow into the oven, unless the flow is limited by a restrictor. This restrictor can hamper the maximum allowable split flow. In the case of the Helium Saver SSL, high split flows remain available because the split is accomplished using nitrogen delivered by separate pneumatics. Development of the Helium Saver SSL is a shining example of how a problem in the back of a person’s mind can sometimes be solved in unexpected ways, just through bouncing ideas off colleagues.
Ed McCauley is a Senior Scientist in Research & Development at Thermo Fisher Scientific, Austin, TX, USA.