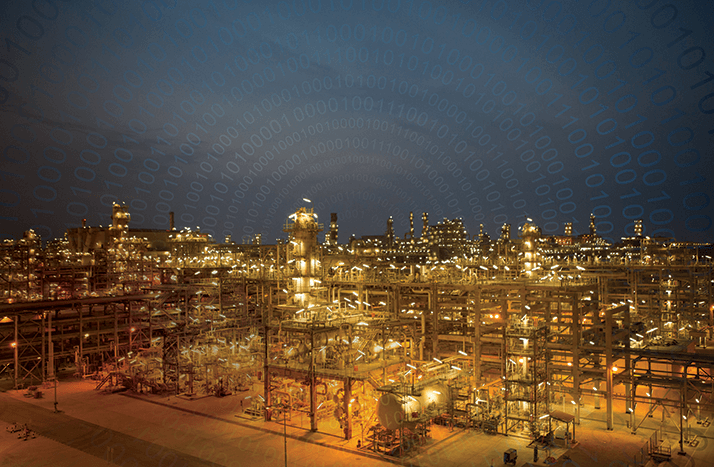
The unprecedented scale of the world’s largest gas to liquids (GTL) plant in Qatar – Pearl GTL – creates a massive business and technology challenge: how can quality be maintained and productivity maximized while managing huge volumes of critical data?
As a senior business analyst for Pearl GTL, I was responsible for managing the laboratory informatics components of a project of unprecedented scale, which required billions of investment dollars and created tens of thousands of jobs during peak construction. Data management was a major priority. To maximize production and allow rapid decisions, we needed consolidated, accurate information available at our fingertips – at all times.
Established by Shell and Qatar Petroleum in 2006, and onstream at the beginning of 2011, Pearl GTL is the world’s largest GTL plant and cements Qatar’s position as the GTL capital of the world. The GTL process converts natural gas to liquid fuels and other products, including gasoil, naphtha, kerosene, normal-paraffin and lubricants. Pearl GTL captures the full value chain, from offshore development and onshore gas processing to the refining of finished products in one project. The project provides the platform for the growth of an entirely new industry with GTL fuels, in particular by opening up opportunities for new markets.
When it comes to illustrating the enormous scale of the project to build the world’s largest GTL plant, the statistics paint an impressive picture. Some two million tonnes of freight were shipped into a dedicated berth at Ras Laffan port adjacent to the plant site. More than 750,000 cubic meters of concrete were poured during construction. And enough steel was being used during the peak construction period to erect the equivalent of two and a half Eiffel Towers a month.
Initially, my major challenge was finding a resilient software solution that supported all of our stringent data and integration requirements – something that could help drive success from the very beginning.
From the start, we knew that we needed a highly sophisticated software solution to manage the interface of a quality control system that receives a constant stream of 34,000 transmitted measurements. These measurements, which include well content, volume, emissions, equipment condition and hundreds of other data points integral to the plant’s operation, needed to be mapped onto the data generated by the laboratory operations. In addition to collection and storage, data also needed to be organized, integrated and analyzed constantly to ensure plant safety, product quality, environmental protection and production efficiency. Furthermore, our solution needed to ensure that Pearl GTL’s labs remained in compliance with requirements such as ISO 17025, an accreditation that sets an international benchmark for running a testing laboratory. It lays out qualifications for suppliers, training, record-keeping, equipment calibration and much more. In the event of an audit, Pearl GTL would need to quickly retrieve and present data proving compliance.
With so many prerequisites for success, we needed a proven solution: a laboratory information management system (LIMS). The right LIMS should present accurate, unbiased information necessary for maintaining the highest standards of safety, regulatory compliance and environmental commitment – all without sacrificing financial performance. But clearly, given the operation’s complexity, not just any LIMS solution would do. In addition to organizing sample results, Pearl GTL’s LIMS would need to be fully integrated with the ability to communicate with a variety of other systems, including operations management, batch tracking and enterprise resource tracking systems. Without such integration, it would be almost impossible to achieve success with a project of this size and scale.
We chose Thermo Scientific’s SampleManager LIMS to manage our state-of-the-art testing laboratories, standardizing it across all laboratory equipment and production systems. SampleManager offered unparalleled support for all of Pearl GTL’s
stringent requirements.
Despite our complex quality, regulatory and interface requirements, we worked with a strong team of people from Thermo Fisher, including Colin Thurston (director of product strategy for informatics). Rolling out the solution across Pearl GTL was seamless, despite some of the LIMS interfaces that were implemented being the first of their kind in any Shell facility.
One of our principal reasons for choosing SampleManager was its ability to integrate with other systems. At Pearl GTL, the LIMS is integrated with an operations management system (known as OTTER), process historian (OSI PI), an oil movement and batch tracking system, laboratory instruments and other production systems. Now, communication between all systems is seamless and bi-directional. And all information necessary to manage complex sample scheduling and stringent safety, quality and regulatory requirements is readily accessible.
The way SampleManager integrates with PI delivers notable efficiencies for Shell and Qatar Petroleum at Pearl GTL. While some other labs manually send test results to operations, technologists and process engineers, the Pearl GTL laboratory results are available to all relevant parties within the PI system as soon as they are authorized in SampleManager. If high accuracy sampling data is important to your job, you can access it through the system in real time.
Other important consumers of lab data within Pearl GTL are users of the oil movement and batch tracking system. When panel operators need to move oil to new tanks in preparation for shipping, for example, they don’t need to wait to be notified of test results, and this minimizes demurrage charges for loading delays. As soon as the results are available from the lab, the LIMS notifies operators through the oil movement system.
The LIMS has also enabled Pearl GTL to go paperless, helping us eliminate many human errors common in paper-based laboratories. Human beings can make an average of 3-6 mistakes for every 1,000 lab readings transcribed, so a sampling program the size of Pearl GTL’s, could lead to hundreds of errors every day. SampleManager solves this problem by integrating lab instruments that automatically transmit data as soon as final results are produced.
SampleManager aggregates all this data and combines it with information collected from other sampling systems, including technicians in the field, enabling Pearl GTL to collate and present a vast array of data in a logical format for managers to analyze and make fast, effective decisions.
Using the OTTER system, all sample points in the field are marked with radio frequency identification tags. When field operators perform sample rounds, a handheld computer guides them to each sample point and then automatically records the required information, such as sampling time, and whether the sampling task is routine or non-routine. The LIMS also transmits safety related information, (such as the sample container to be used and special instructions for sampling) to the handheld computers to ensure the wellbeing of staff. As the LIMS is fully integrated with OTTER, the data collected is instantly transferred to SampleManager from the field for analysis by managers or technicians back in the lab, which also saves Pearl GTL an estimated 2,400 working hours per year.
It’s interesting to note that all the benefits we achieved by implementing SampleManager are completely transferable to other industries, which Colin can explain in more detail.
Ajith has outlined nicely the implementation of SampleManager LIMS at Pearl GTL, an enormous accomplishment for both Shell and Thermo Fisher alike. Among the most important benefits of a fully integrated informatics solution is the agility gained in moving assets, reassigning personnel or streamlining production. In essence, the LIMS gives the business the ability to make more timely decisions.
The same principles are echoed in many other industries, for example, downstream of the oil refinery at modern chemical manufacturers. The need for agility is especially true in the production of fine and specialty chemicals, where plants may change over production lines weekly, sometimes even daily. Within these highly flexible environments, laboratories responsible for quality, safety and efficacy of finished products must be equally flexible, which is no simple task.
In the chemical manufacturing lab, LIMS isn’t just the first step, it’s the most important step towards achieving the agility required to meet more precise customer demands and more stringent regulatory requirements. Once in place, the business isn’t simply capturing and collecting data; it’s making that data actionable across the enterprise. With the LIMS enabling this type of data mining, management can move more quickly to respond to market trends or new regulations or to recognize and capitalize on cost-saving or margin-growing opportunities.
For businesses to compete in manufacturing, they need to liberate the insights that are too often kept in silos across the site or around the world. Opening up these vast stores of knowledge to the benefit of the enterprise can improve manufacturing technology in new ways. Your laboratories can become real growth drivers for business transformation and enable your business to rapidly capitalize on new growth opportunities and build lasting value, customer loyalty and security for employees.
Ajith Kumar is a senior business analyst at Pearl GTL, Qatar, and Colin Thurston is informatics project director at Thermo Fisher Scientific.