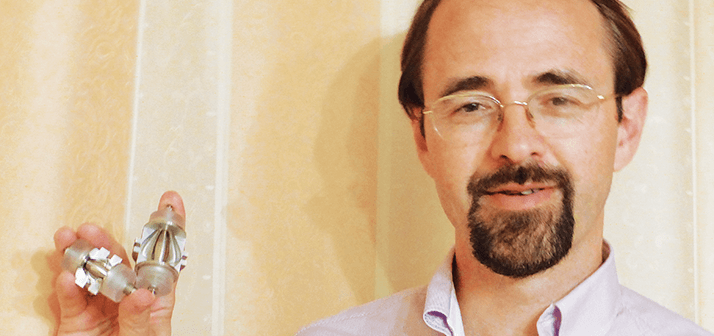
Thermo’s research elite arrived for a demonstration of the Orbitrap.
I switched the instrument on, only to discover that the turbopump was dead – a rare event, and difficult to repair. The delegation was scheduled to leave at noon the next day, so time was of the essence. I ran over to Thermo Masslab, shouting, “Please, please, give me a pump.” They had one that I could substitute for ours, which was a stroke of luck. I ran back to the lab and used the night hours to install the new pump and put the instrument back together. I arrived at the lab early the next day to make some final preparations. To my despair, I discovered an electrical short inside the vacuum. I couldn’t break the vacuum because there would be no chance of measuring anything at all. This, for me, is the lowest point of the entire story. The instrument was too big to be picked up, so I started to shake the chamber containing the Orbitrap analyzer – far from recommended behavior when dealing with turbopumps. Yet, somehow, the shorted wires inside the vacuum moved away from each other and the system started to operate. When the delegation arrived, they witnessed high resolution and high mass accuracy. All in all it was very lucky and, in hindsight, rather fun; but it was also very bad practice – people get sacked for doing that sort of thing.
That was just two days from the many years that I’ve spent developing Orbitrap but it encapsulates the whole story. We knew from the outset that it wouldn’t be easy but had hoped that once we climbed the first “mountain” everything would get more straightforward; however, what we found when we reached that first summit was a whole range of higher mountains stretching one after the other into the distance. Year by year, one by one, we conquered them. Only later did we think about just how close we were to falling off the cliff face: many times we were hanging by a thread but, possibly because we were moving so quickly, we didn’t get easily discouraged. But let’s go back to the beginning…
Small company, big ambitions
I set out with very little knowledge – just optimism based on the absence of negative information. The seed of motivation was sown in my early days at HD Technologies in Manchester, UK, which I joined officially in 1996. As a start-up, HD was fighting just to ensure survival and yet we were very ambitious, convinced that this small company could contribute something significant. Everything was still relatively new to me: I only arrived in the UK from the former Soviet Union with my family in August 1994. HD Technologies greeted me with a distinct air of excitement and creative freedom. We had so many ideas that we could implement and realized that we needed something that was thoroughly unusual, something that no other company could develop. When I told him of my dreams, Steve Davis, the head of the company, said to me, “Alexander, it needs to be the ideal mass spectrometer, with the resolution of Fourier transform ion cyclotron resonance (FT ICR), the sensitivity of linear time-of-flight (TOF) and the size and capabilities of a quadrupole ion trap.”
I knew Steve from the early nineties when he was working at Kratos Analytical (now Shimadzu), also in Manchester. He was the manager of MALDI TOF and they had just released the Compact MALDI III instrument. Steve had big plans and urgently needed someone with ion-optical experience. At the time, I was just traveling around after my PhD. Because I didn’t have any money, I would arrange with universities to give a lecture and they would pay for my stay and train ticket to the next venue. One of the presentations was at the University of Salford and, although Steve wasn’t there, his colleagues were; thinking that I sounded like an instrumentation guy, they suggested that I talk to their manager. I was still in the UK when Steve returned from Australia. Our meeting must have gone pretty well because he asked me to become a consultant for Kratos. Unfortunately, however, Shimadzu reorganized Kratos and, instead of hiring me, shut down all magnetic sectors (indeed, they temporarily stopped all R&D projects in favor of production support).
This turn of events pushed Andy Hoffman, who worked on the electronics side, and Steve Davis to make an important decision. They used a request for voluntary redundancy to resign, received redundancy money, and set up their own company – HD Technologies. For the first two years, they didn’t have the money to hire me, but they helped me to get a postdoc position. During that time, we often met together, discussing plans, and finally they managed to secure sufficient contracts to get me on board. The deal was that from 9am to 5pm (actually, it was more like 9am to 9pm) we would focus on contract projects, but that we would use our weekends to work on something “out of the box”. I guess it was the kind of creative, progressive atmosphere that is typical of small companies that succeed; yes, we needed to find money for the next month but, at the same time, we knew that we needed to do something unusual to break that vicious cycle. Soon I started talking about an idea I’d had that used my knowledge of TOF technology.
I have to admit that 20 years ago I didn’t know anything about running instruments properly; my PhD was mainly theoretical but the interaction with the Kratos Analytical team taught me that, if I stayed that way, there was little room for me in the lab. I started out pretending that I knew what I was doing but I learned quickly. Working with my hands at HD Technologies gave me a practical understanding of real-life problems, and it was while doing this that my ideas about a new mass spectrometer started to turn into something more concrete.
A typical conversation would have me proudly announcing to my colleagues, “Look! I have a trap – we just need to inject ions, but basically it’s done!,” followed by their skeptical cross-examination about how the ions would get inside. “What? Isn’t it clear?” I would ask. After explaining in more detail, they might or might not agree (in actual fact, getting ions into the trap is more complicated than analyzing them once they are there). I listened to every query and challenge, went away to think about them, and then came back with another idea. Then they’d laugh and tell me I hadn’t thought about another aspect – pumping, for example. We went back and forth this way, with me accumulating a thick stack of papers filled with formulae and calculations. In hindsight, despite the tough time that they gave me, my colleagues were too optimistic: reality would be much tougher. Nevertheless, these early calculations were enough to win a UK Smart (Small Firms' Merit Award for Research and Technology) grant. It was only about £50,000 but it allowed us to make a start and, perhaps more importantly, it set a fixed deadline to deliver something. The project was assigned development time, allowing me to work harder on it. If this had not happened we would have probably been consumed by the everyday, routine contracts.
ASMS Game-changer
When we started to design the instrument there were further clashes between theory and reality, requiring us to adapt to all kinds of problems on the fly. In fact, we didn’t bother to test the first prototype because by the time the design was finished and the parts were made, it was clear that we didn’t have the right electronics for it. I lacked electronics experience and designed a very simple solution but it is still used today to drive the central electrode, so it turned out to be very robust!
Our perseverance eventually yielded a working experimental set-up. Creating ions was easy because of our MALDI TOF experience using lasers, and when you have pulse packets it’s easier to capture the ions in the trap. We obtained our first spectra in October 1998. The system produced increasingly high resolution, reaching 150,000 by July 1999, at which point we presented our proof-of-principle at the American Society for Mass Spectrometry (ASMS) meeting in Dallas, Texas. They were pretty simple data from unreliable and unstable equipment, but they showed off the unmistakably high resolving power of the “Orbitrap” (see “What’s in a Name?”). The major work – to commercialize the concept – was still ahead of us.
Besides our presentation of Orbitrap, the ASMS meeting proved important in another way. We presented several additional projects – MALDI-TOFs, GC-TOFs and so on – that generated interest from the “big guys”, including Thermo, and we told people that we couldn’t develop Orbitrap technology on our own. The consequence was that we started conversations with five major mass spectrometry companies. But the more discussions we had, the more the objections and limitations mounted up like another range of mountains to be scaled (see “Reasons Why Orbitrap Should Not Work”, page 30). The main limitation was that it could not be used for continuous ion sources like electrospray, which is the main workhorse of mass spectrometry; but the really scary thing was that all of the objections were justified, including quite a number that we hadn’t thought of ourselves.
As daunting as it was, however, knowing the challenges was a good thing. It meant that we could begin on the long road to a commercial product. Each challenge became a development project in its own right.
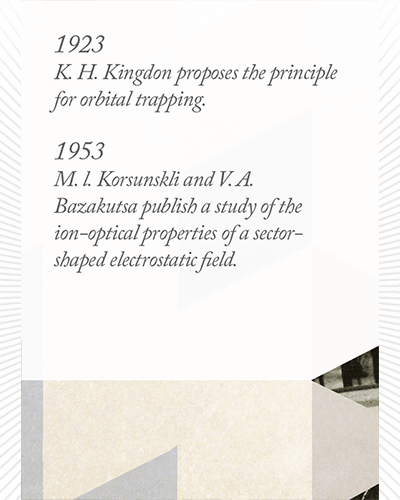
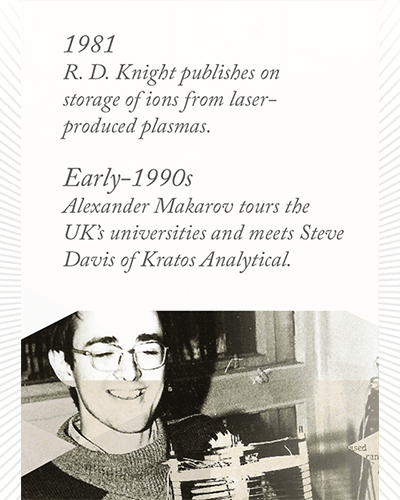
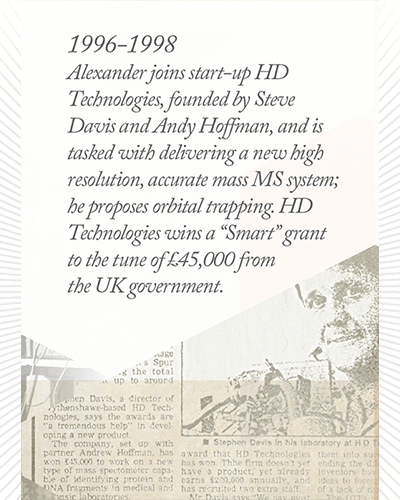
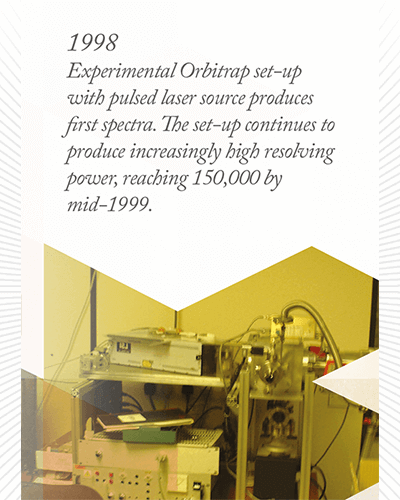
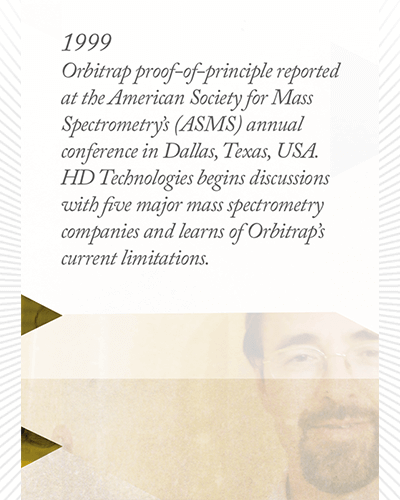
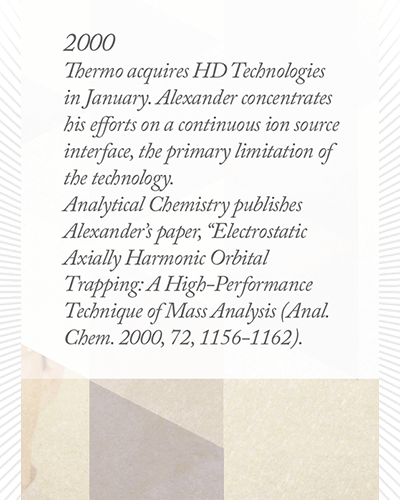
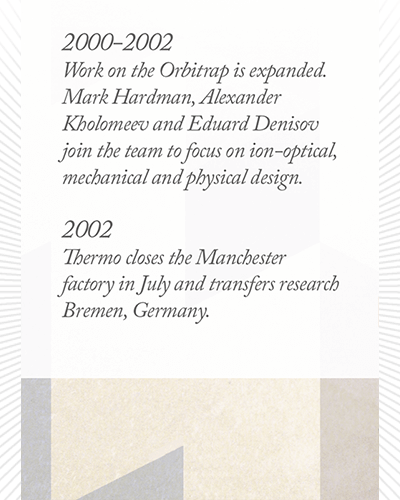
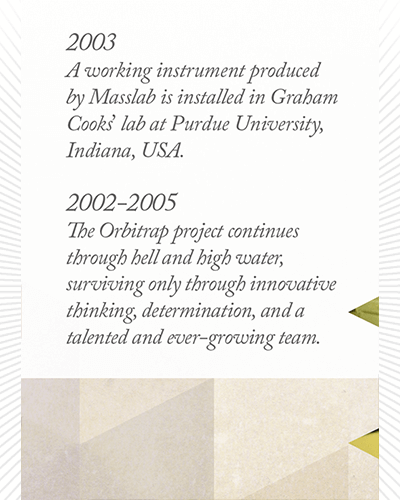
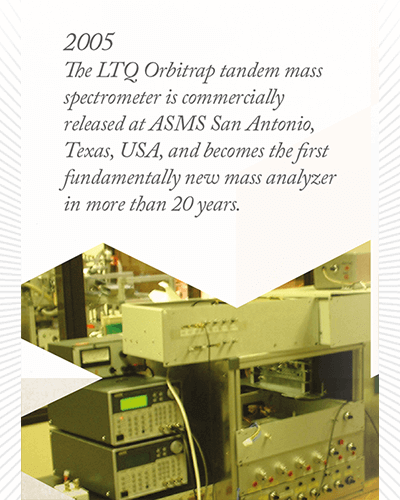
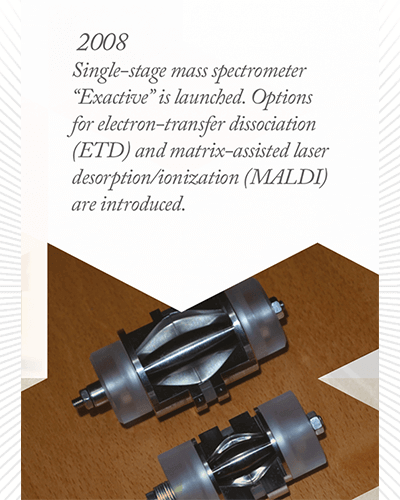
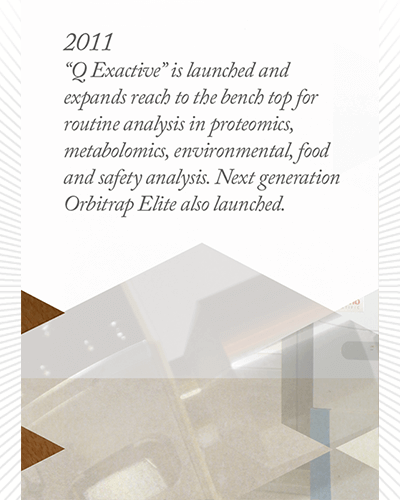
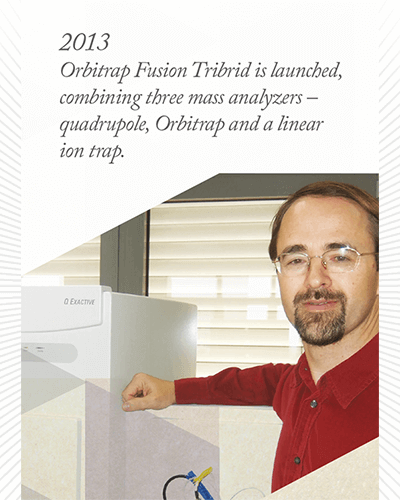
I set out with very little knowledge – just optimism based on the absence of negative information. The seed of motivation was sown in my early days at HD Technologies in Manchester, UK, which I joined officially in 1996. As a start-up, HD was fighting just to ensure survival and yet we were very ambitious, convinced that this small company could contribute something significant. Everything was still relatively new to me: I only arrived in the UK from the former Soviet Union with my family in August 1994. HD Technologies greeted me with a distinct air of excitement and creative freedom. We had so many ideas that we could implement and realized that we needed something that was thoroughly unusual, something that no other company could develop. When I told him of my dreams, Steve Davis, the head of the company, said to me, “Alexander, it needs to be the ideal mass spectrometer, with the resolution of Fourier transform ion cyclotron resonance (FT ICR), the sensitivity of linear time-of-flight (TOF) and the size and capabilities of a quadrupole ion trap.”
I knew Steve from the early nineties when he was working at Kratos Analytical (now Shimadzu), also in Manchester. He was the manager of MALDI TOF and they had just released the Compact MALDI III instrument. Steve had big plans and urgently needed someone with ion-optical experience. At the time, I was just traveling around after my PhD. Because I didn’t have any money, I would arrange with universities to give a lecture and they would pay for my stay and train ticket to the next venue. One of the presentations was at the University of Salford and, although Steve wasn’t there, his colleagues were; thinking that I sounded like an instrumentation guy, they suggested that I talk to their manager. I was still in the UK when Steve returned from Australia. Our meeting must have gone pretty well because he asked me to become a consultant for Kratos. Unfortunately, however, Shimadzu reorganized Kratos and, instead of hiring me, shut down all magnetic sectors (indeed, they temporarily stopped all R&D projects in favor of production support).
This turn of events pushed Andy Hoffman, who worked on the electronics side, and Steve Davis to make an important decision. They used a request for voluntary redundancy to resign, received redundancy money, and set up their own company – HD Technologies. For the first two years, they didn’t have the money to hire me, but they helped me to get a postdoc position. During that time, we often met together, discussing plans, and finally they managed to secure sufficient contracts to get me on board. The deal was that from 9am to 5pm (actually, it was more like 9am to 9pm) we would focus on contract projects, but that we would use our weekends to work on something “out of the box”. I guess it was the kind of creative, progressive atmosphere that is typical of small companies that succeed; yes, we needed to find money for the next month but, at the same time, we knew that we needed to do something unusual to break that vicious cycle. Soon I started talking about an idea I’d had that used my knowledge of TOF technology. I have to admit that 20 years ago I didn’t know anything about running instruments properly; my PhD was mainly theoretical but the interaction with the Kratos Analytical team taught me that, if I stayed that way, there was little room for me in the lab. I started out pretending that I knew what I was doing but I learned quickly. Working with my hands at HD Technologies gave me a practical understanding of real-life problems, and it was while doing this that my ideas about a new mass spectrometer started to turn into something more concrete. A typical conversation would have me proudly announcing to my colleagues, “Look! I have a trap – we just need to inject ions, but basically it’s done!,” followed by their skeptical cross-examination about how the ions would get inside. “What? Isn’t it clear?” I would ask. After explaining in more detail, they might or might not agree (in actual fact, getting ions into the trap is more complicated than analyzing them once they are there). I listened to every query and challenge, went away to think about them, and then came back with another idea. Then they’d laugh and tell me I hadn’t thought about another aspect – pumping, for example. We went back and forth this way, with me accumulating a thick stack of papers filled with formulae and calculations. In hindsight, despite the tough time that they gave me, my colleagues were too optimistic: reality would be much tougher. Nevertheless, these early calculations were enough to win a UK Smart (Small Firms' Merit Award for Research and Technology) grant. It was only about £50,000 but it allowed us to make a start and, perhaps more importantly, it set a fixed deadline to deliver something. The project was assigned development time, allowing me to work harder on it. If this had not happened we would have probably been consumed by the everyday, routine contracts.
When we started to design the instrument there were further clashes between theory and reality, requiring us to adapt to all kinds of problems on the fly. In fact, we didn’t bother to test the first prototype because by the time the design was finished and the parts were made, it was clear that we didn’t have the right electronics for it. I lacked electronics experience and designed a very simple solution but it is still used today to drive the central electrode, so it turned out to be very robust! Our perseverance eventually yielded a working experimental set-up. Creating ions was easy because of our MALDI TOF experience using lasers, and when you have pulse packets it’s easier to capture the ions in the trap. We obtained our first spectra in October 1998. The system produced increasingly high resolution, reaching 150,000 by July 1999, at which point we presented our proof-of-principle at the American Society for Mass Spectrometry (ASMS) meeting in Dallas, Texas. They were pretty simple data from unreliable and unstable equipment, but they showed off the unmistakably high resolving power of the “Orbitrap” (see “What’s in a Name?”). The major work – to commercialize the concept – was still ahead of us. Besides our presentation of Orbitrap, the ASMS meeting proved important in another way. We presented several additional projects – MALDI-TOFs, GC-TOFs and so on – that generated interest from the “big guys”, including Thermo, and we told people that we couldn’t develop Orbitrap technology on our own. The consequence was that we started conversations with five major mass spectrometry companies. But the more discussions we had, the more the objections and limitations mounted up like another range of mountains to be scaled (see “Reasons Why Orbitrap Should Not Work”, page 30). The main limitation was that it could not be used for continuous ion sources like electrospray, which is the main workhorse of mass spectrometry; but the really scary thing was that all of the objections were justified, including quite a number that we hadn’t thought of ourselves. As daunting as it was, however, knowing the challenges was a good thing. It meant that we could begin on the long road to a commercial product. Each challenge became a development project in its own right.
The name Orbitrap actually appeared much earlier than the technology itself. When I first showed the principle of trapping to my colleagues in the autumn of 1996, they asked “so… what is it?” I replied that it was an electrostatic trap, and we decided that it needed a name. I don’t remember exactly when I came up with the term Orbitrap, but I think it was during some holiday time when my mind was mulling over the problem. I knew that the name needed to include “trap” but I didn’t know what to add to it. I recall writing down several word combinations but they didn’t go well together. Then I thought well, ions are orbiting, so it’s an orbital trap: orbitrap. I went back to colleagues with the name and they agreed that it was short and clean. Later, when I titled my first paper, “Orbitrap: a new high-performance technique for mass analysis,” a reviewer insisted that the name was wrong because the ions are not separated by their orbit but by frequencies of axial oscillation. The axial component should be reflected, the referee said. I was upset that I had to replace the title with some dull technical term, but included Orbitrap somewhere less prominent in the text. Eventually everyone started using it, and it then became a trademark. At some point after the launch there were a few derogatory comments about the name, but Orbitrap caught on like wildfire and any criticism disappeared.
Thermo was the company most interested in collaborating, firstly, because of our TOF technology and secondly, because they already knew from previous interactions that we were innovative, serious about development, and that we had fun at work. Thermo acquired HD Technologies in January 2000 – just before the Dot-com bubble burst. Pretty lucky. While Orbitrap technology wasn’t actually the major reason for Thermo’s acquisition, we still received a due diligence visit from Thermo’s top four research scientists (George Stafford, Jae Schwartz, John Syka and Mike Senko) prior to the purchase in November 1999 – the story that opens this article. They were all extremely interested in seeing the technology in action and (following the secret dead pump, electrical short and analyzer-shaking episode) were thoroughly impressed by what they saw. Very lucky.
In fact, we’d had more luck on our side without knowing it. All of our original experiments had been conducted with the original set of electrodes. In parallel to instrument development, we had been trying to make a second set of electrodes and were failing miserably. The working electrodes had been made on a brand-new lathe by a small company nearby; we were never able to produce working electrodes with any lathe, whatever its precision, despite spending years and years trying. Now, of course, almost every electrode that is machined works within specification, but back then that was simply impossible. Had it not been for that original freak success, we wouldn’t have the Orbitrap today… At other times, perseverance and ingenuity kept us afloat. On the problem of interfacing Orbitrap with continuous ion sources, we’d spent ten times more effort than anticipated, encountering numerous problems. Each time, just when it seemed like the whole project would be shuttered, we would come up with some alternative idea. This was because, throughout, development was progressed along parallel tracks: a “main track” where we were going at full speed using maximum resources, and a “back-up track”, which was usually higher risk. Several times over the course of the project, the seemingly guaranteed, straightforward solution failed and we had to resort to the fallback – it’s a testament to our planning and to the team, which was growing with new talent that included Mark Hardman, Alexander Kholomeev and Eduard Denisov. The eventual solution to the continuous accumulation problem was the C-trap, a novel storage device.
► It is not possible to provide ion packets with the required spatial and temporal parameters for continuous ion sources
► The tolerance requirements on the electrodes are not realistic
► Injection and central slots will ruin resolving power and mass accuracy
► The vacuum requirements are ridiculous and cannot be met
► Ions can not be injected with high efficiency
► A wide mass range cannot be injected and captured
► The image current preamplifier will be destroyed by pick-up during injection
► Noise from the high voltage power supply will overwhelm the preamplifier
► Surface potentials will disturb and scatter ions
► Mass accuracy will be poor because of voltage drift and noise
► Large ion numbers cannot be properly injected or analyzed
► The electrode shape, rotational and radial frequencies will cause unmanageable mass-dependent harmonics
The factory in Manchester was shut down in July of 2002 and the project moved to Bremen, Germany. My family stayed in Manchester so I had to commute for several years. Two people from my group moved to Bremen to work on the project full-time and we got excellent support from the local management, particularly Reinhold Pesch, R&D director at the time. Both he and Bremen site director Juergen Srega gave us whatever we needed, whenever we needed it. They understood that the only way to move forward was to work with the highest intensity possible, which is why they gave us their best scientists and best project manager – Stevan Horning. The other side of that arrangement is that we needed to show that we could deliver what we promised. Wilko Balschun and Oliver Lange made up the core group of five, which would stay together to deliver Orbitrap. We benefitted hugely from the decades of acquired experience at Bremen but, whatever the size of the organization, it’s the core team that matters. You need enthusiasts that are willing to fight and die for the project and the high risk of failure helped fuel that mentality. Personally, I felt another source of urgency: since I couldn’t continue commuting indefinitely, I needed to produce results! It just wasn’t civilized living between two countries in cities that lacked a direct flight between them. However, although it was personally frustrating, it was successful from a work perspective. When in Bremen, I spent my time in the lab; back home in Manchester I had space for modelling, designing and thinking through experiments. We gradually plucked a route of success through a more abundant series of failures. The highest workload came in the run-up to the commercial release of the LTQ Orbitrap tandem mass spectrometer at the June 2005 ASMS conference. Nowadays, a small team like ours would never attempt such a launch. The progression from breadboard to prototype to pilot, and so on, was taxing on everyone – and resulted in a few years of supporting unusual situations with customers. However, the sheer improvement in performance that Orbitrap delivered more than justified these original teething troubles; it was, after all, the first fundamentally new mass analyzer for more than 20 years.
Fifteen or 20 years ago, a small group of colleagues set out with the spirited intention of moving the needle – doing something that would really change the face of our industry. What I discovered is that it’s one thing to have a scientific curiosity that everybody loves, it’s quite another to deliver something to labs, where it matters. We did it. And, unusually, the entire development, from proof of principal to mass production, took place within one group. After the Orbitrap instrument was launched, it was extremely rewarding to witness the improvment in results that researchers achieved and to see some of their technical problems solved. At launch, the LTQ Orbitrap was the most expensive system on the market and, like most new technology, it penetrated the early adopters first and only much later did it enter more routine labs. It’s always difficult to see the full impact from the inside; when you are fighting for something from morning until night you don’t always hear what’s happening in the field. Only later did I understand the scale of change. Competitors were generally astounded by Orbitrap technology. They respected the science fully and always expressed their highest regards for the entire technology. And their reaction to the introduction of Orbitrap helped to accelerate the entire field as it woke them up and got them moving forward. I believe that mass spectrometry users have much better technology now than they would have had without our product – whether they are Orbitrap users or not.
I am sometimes asked if I am surprised that Orbitrap technology is still relevant today. My answer is no, I am not; actually, I believe that the Orbitrap age is only just beginning. The new Fusion Tribrid obviously represents the pinnacle of Orbitrap development to date. It’s the tip of the pyramid and the base is rapidly expanding with routine instruments, like the Exactive and Q Exactive. The pyramid will continue to grow by enabling new applications, to the point where high resolution and accurate mass become as routine as nominal mass analysis by triple quadrupoles. I believe that environmental, food, forensics, toxicology, doping – in fact, all analyses – should be high resolution and accurate mass in the end. To achieve this, two main challenges must be overcome. First, we need to constantly crank up performance to match the increasing complexities of samples and increasing expectations of users (and keep up with any competition). Second, we have to make the technology both bulletproof and routine in operation. Today, quadrupole technology is routine, but in the 1950s and 60s it was the top end, highest of high tech, with only a few people able to make it work. That’s the transition that Orbitrap technology is going through now. We need to switch from the current, relatively fragile and difficult-to-tune machine, to an instrument that “just works”. These two goals – performance and usability – are demanding, but achieving them will reap rich rewards from a massively increased user base.
So far, Orbitrap is used mainly with electrospray and atmospheric ion sources, but in the future it will be used with all other ion sources. My main interests and expectations are in the clinical analysis of peptides and proteins – the entire promise of proteomics is actually strongly linked to Orbitrap technology. While the field is not yet delivering on the optimistic promises of ten years ago, both proteomics and clinical analysis are currently much further ahead than if we had continued the linear development of the early days. I feel lucky to have gone through all phases of the development of Orbitrap. Today, I am as excited about the technology as I was in the beginning, but perhaps in a different way. Plus, we have the challenge to produce something that’s as good as, or even better than, Orbitrap; that will be difficult! For now, I am focused in part on front-end development with ion sources and research into new types of analyzers. I am also passionate about improving the use of analytes. At the moment we throw most of them away but we should be able to get to the point where we use analytes completely. These are tough challenges but the success of Orbitrap has given me some of the resources and belief that I need. If only I had more time! University collaborations, conferences and management all compete for attention, which leaves only a small percentage to concentrate on these hopes for the future. My big dream is that one day every hospital will have an Orbitrap mass spectrometer – that would really have the greatest impact on society. There’s a long way to go and, as proven by this story, whether it happens or not depends on many different circumstances, but also on me.
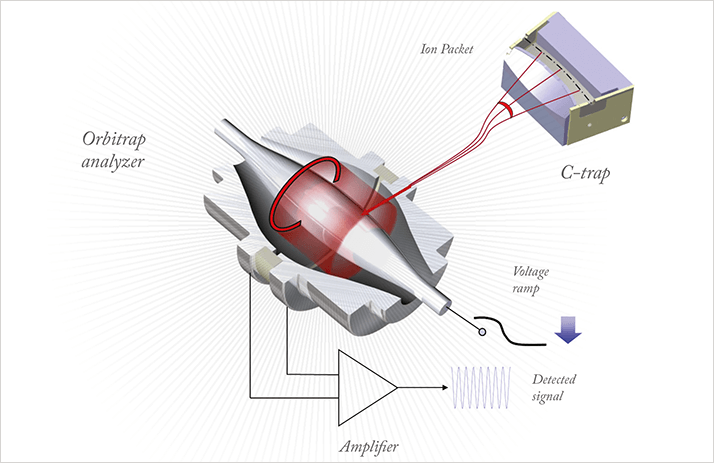
The Orbitrap consists of an outer barrel-like electrode and an axially symmetrical central spindle-like inner electrode. To inject ions, the field between the electrodes is first reduced. The ions enter the field and are squeezed closer to the centre of the trap by an increasing electric field, like stars to a black hole. After the mass range of interest has entered the Orbitrap, the voltage is stabilized and detection may take place. The ions move along complicated spiral cycles that have three components:
- rotational movement
- radial movement
- axial oscillations along the central electrode
Alexander Makarov is Director of Research, Life Science Mass Spectrometry, Thermo Fisher Scientific, Bremen, Germany.