Among analytical instruments and techniques, one stands above all others in terms popularity: gas chromatography (GC). This so-called ‘mature’ technique is ubiquitous in analytical labs and most often turned to for a first evaluation of sample composition, even though it is appropriate for only 10 percent of potential sample types. There are good reasons for GC having such clout. It is fast (meaning cost-effective), boasts high resolution (meaning unambiguous results), and is highly evolved (meaning relatively easy to use).
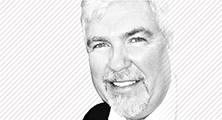
While the theory has been understood for years and the field is in many respects ‘mature’, GC is still an evolving analytical practice from one perspective: the instrument itself. As I shall illustrate here, each component of a chromatograph has a crucial role to play in constantly improving the generation of accurate, cost-effective data.
Take the heart of GC analysis: the separation column. Do you know how the columns that you rely upon were tested prior to packaging and delivery to your laboratory? I find it incredible that some people happily say that a column made by manufacturer A is “just like” that of manufacturer B without serious thought. Any difference is critical because during the course of a GC analysis, solutes have over 50 times the surface exposure in the column compared to the liner and injection port seal.
Dozens of process steps are involved in the manufacture of a capillary GC column, each with a list of parameters that must be optimized to produce a uniform, stable, inert stationary phase. At my company, Agilent Technologies, in-process evaluations are performed throughout the process and, once produced, every individual column is tested. Testing each column rather than batch testing is daunting, especially give that we produce thousands of columns in hundreds of different configurations on a weekly basis. However, we have ample evidence that in batches of columns that meet our specifications, there can be one column that does not meet the highest standards.
The quality of GC results emerge from a combination of multiple chromatographic parameters, including internal diameter (ID), retention factor, phase ratio, theoretical plates, bleed, and tailing factor. Most of these parameters will be very familiar to seasoned chromatographers but the importance of certain performance attributes may be underestimated. Inertness is a good example. In chromatography, inertness is the absence of reactive sites in the flow path towards the sample solutes. Stated simply, what goes in the GC, comes out. It is important to know not only what you are ‘seeing’ in the data, but also what you are not seeing. This is particularly important in the analysis of untargeted analytes, but also in routine analysis for the most reactive target solutes.
Our focus on improving column inertness goes back more than a decade. It was in this regard that in 2002, the co-founder of J&W Scientific, my mentor the late Prof. Walt Jennings came into work one day and proclaimed to the scientific staff that we were no longer trying to make better products at J&W; just the same old good products we had become good at making. To him, quality was always about improvement. He told us, “When the majority of the columns you make are passing your QC test, it is because your test isn’t stringent enough.” He was so ardent about this that in 2004, Walt challenged the chromatography community to become concerned about what was being missed in analyses due to solute losses by inadequate GC flow path inertness (1). We set out to test how “bad” the columns of the time were (2) and found that, while they were passing our already stringent QC tests, there was room for improvement. Generating that performance improvement has taken time and expertise. While the measurement of theoretical plates and retention factors are straightforward ways to evaluate and compare individual columns, the chromatographic measurement of inertness is complicated by the solutes – and how much of each is being analyzed – and the conditions of the analysis. Furthermore, it was essential to ensure that any performance gains were not at the expense of performance loss in another parameter. For, example, some column-makers thermally condition their products at high temperatures for extended periods. This improves column bleed background, but column inertness is compromised. By adhering to good scientific observation, focusing on quality in the manufacturing environment, and applying sound chemistry solutions, real improvements have been made, as evidenced by our Ultra Inert columns. This process continues on a daily basis: the only way a manufacturing facility can be competitive is to constantly apply scientific innovation on the factory floor and build products to demand. Quality must be an ongoing mission and it must be built-in, not achieved by chance.