The Problem
How can the components of oily residues in LPG, and the likely source of these contaminants, be identified using a fast, robust method?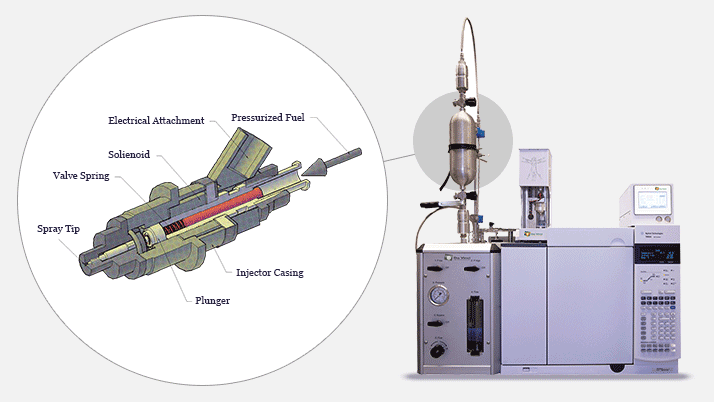
If you work in a petrochemical plant, a refinery, in LPG production, shipping, handing, or at an analytical laboratory charged with LPG analysis, you’ll know a thing or two about oily residues—both the associated analytical problems and the negative impact they can have on machinery. LPG is predominantly a mix of propane (C3H8) and butane (C4H10). Compositional analysis is generally performed using GC-based methods, but propane and butane (C3/C4) sample streams may also contain contamination from soluble hydrocarbons from C10 up to C40 – the typical constituents of oily residue. A number of conventional methods for the analysis of oily residues in LPG have been set out by standards institutions, such as ASTM and CEN (namely, ASTM D2158, EN 15470 and EN 15471). These methods have been in use for many years but they have known limitations. Lab managers must deal with the fact that they are labor intensive, time consuming and hazardous. In addition, the tests are environmentally unfriendly, requiring the evaporation of 100g to 2 kg of LPG. Equally damning, they offer no way of identifying the source of contamination, which makes troubleshooting difficult. In 2007, Da Vinci Laboratory Solutions (DVLS) was approached by Shell Global Solutions in Amsterdam, the Netherlands, to work in close cooperation on the development of an alternative solution for the analysis of oily residue in LPG using gas chromatography (GC). In particular, the analytical problem that we were tasked with was to quantitatively detect high boiling components in low-boiling matrices. For some applications, a gas chromatographic solution was available, but sample introduction into the analyzer was a weak point, because uncontrolled amounts of heavy components were retained and/or absorbed by the transfer lines from the sampler to the analyzer.
The Good:
Liquefied petroleum gas has become something of a “darling” alternative fuel in the last years. Why? It’s more cost effective than its cousins, gasoline and diesel, and much more environmentally friendly. In comparison to gasoline, the flammable mixture of hydrocarbons that make up LPG produce 50 percent less carbon monoxide, 35 percent less nitrogen oxides and have just half of the lower ozone-forming potential. Furthermore, its price is less dependent on crude oil, meaning that LPG is more robust in the marketplace. LPG is wonderfully versatile, and can be used for heating, power generation, refrigeration, cooking and vehicles.
The Bad:
LPG is prone to oily residues that accumulate to form troublesome deposits that corrode or plug fuel filters, pressure regulators, fuel mixers or control solenoids. It can become contaminated by oily residue in just about any part of the production and transportation lifecycle. Transport contamination alone can occur in shared pipelines, valves and trucks used for the distribution of other products.
The Ugly:
Until recently, laboratory analysis of LPG contamination had proven to be labor intensive, time consuming, environmentally unfriendly and even hazardous. In addition, there was no way to obtain an indication about the source of the contamination, a fact that left LPG stakeholders with question marks as to how to fix the problem.
Through our discussions it became clear that the market needed a safe, reliable and robust method to determine LPG residue – qualitatively and quantitatively – in less than half an hour. This required the development of a high-pressure injection system with the following qualities:
- Large volume injection
- Ability to handle pressure up to 25 Bar
- No absorption
- No discrimination
- No fractionation
- Sample size capabilities from 5-100 µl
- Low or no dead volume
- Low maintenance and user-friendliness
- The fast turnaround of container cargo (be it by truck, barge or pipeline).
- The elimination of unnecessary LPG evaporation, to reduce environmental impact.
- The incorporation of a proven sample introduction device for high-pressure on-column injection.
In close collaboration with Shell, Da Vinci’s director of R&D Lenny Kouwenhoven and her team were inspired by the well-proven gasoline direct injector (GDI) used to inject fuel into the automotive engine combustion chamber. The prototype injector used a modified GDI connected to a standard GC injector needle that could be inserted into existing large-volume, on-column GC injection systems.
The DVLS Liquefied Gas Injector (LGI), unveiled in 2010, can inject liquefied gases at room temperature directly on-column at up to 25 bar. Solenoids with millisecond timing activate to transfer the pressurized sample through the needle. A vapor exit flushes the LPG light end fraction and the oily residue remains in the column and is separated in order of boiling point. The result is reported as a concentration in mg/kg (mass ppm). The analysis range covers 10–600 mg/kg with a repeatability of below 5% and a relative standard deviation of between 2.4 and 4.7%. The required analysis time is less than 30 minutes. In summary, the LGI has many desirable traits:
- Direct on-column injection on to GC up to 25 Bar
- Faster than conventional methods
- Repeatability less than 5%
- Proven GDI technology
- Sample size from 5–100 µl
- Results reported in mg/kg
- Chromatogram indicates the source of the contamination.
- Environmentally friendly (eliminates the evaporation of large volumes of LPG into the atmosphere)
- Directly addresses safety concerns for lab personnel (no open air evaporation of LPG)
Company: Shell Global Solutions Founded: 1900 Headquarters: The Hague, The Netherlands CEO: Peter Voser Number of employees: 90,000
Company: Da Vinci Laboratory Solutions Founded: 2000 Headquarters: Rotterdam, The Netherlands Managing Director: Willem van Raalte Number of employees: 32
Project Team Leader: Lenny Kouwenhoven, Director of R&D Project Team Members: Anita R (application specialist), Cees Oudijn (product manager), Edwin Beekwilder (R&D manager) and Frank van Schooten (R&D engineer).
Developing a new GC injector that addressed the needs of the industry was a good first step. But equally important was working with standards organizations to determine whether a new method would help customers in the analysis of LPG residues. This proved to be the case and in December 2011, ASTM released a new method: “Residues in Liquefied Petroleum Gases by Gas Chromatography with Liquid, On-column Injection” (ASTM D7756-11). The benefits of ASTM D7756-11 include:
- no open air evaporation of LPG
- analysis in under 30 mins
- effective waste management
- standard GC analysis
- indication of contamination.
When the Shell team first called, we had no idea about the true potential of the solution. Then, customers started requesting support in related application areas. Our development team is currently working on methods of analysis for:
- Di-isopropanolamine (DIPA) in LPG
- 4-Vinylcyclohexene (VCH) in butadiene
- 4-Tert Butylcatechol (TBC) in butadiene
- n-Methyl-2pyrrolidone (NMP) in butadiene
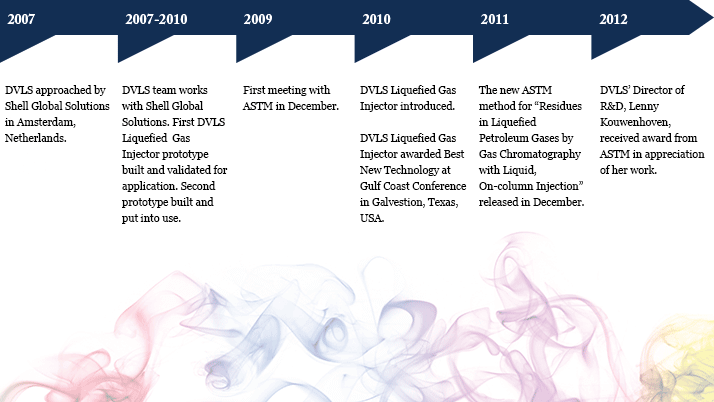
Following several management positions in the laboratory instrument manufacturing sector, Willem van Raalte established Da Vinci Europe Laboratory Solutions B.V. in 2000 to provide laboratory support in the Benelux region. True to his entrepreneurial spirit, van Raalte quickly realized his company could answer additional market demands. “As our customers needed more than just support and instruments, Da Vinci moved towards providing analytical solutions.” Twelve years later, and Da Vinci has expanded its offerings to a worldwide customer base through a robust network of partners.
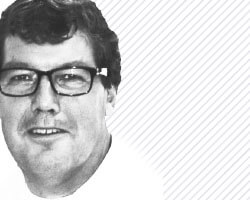
Willem van Raalte is Managing Director of Da Vinci Laboratory Solutions.