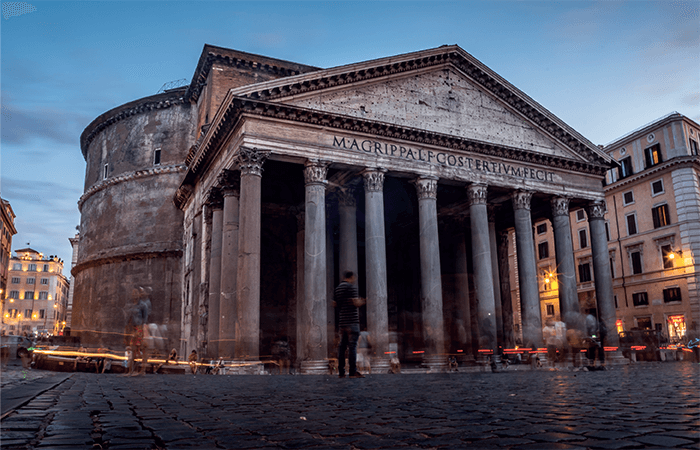
As the world's largest unreinforced concrete dome, the Pantheon is unequivocal proof of the excellent engineering skills of the ancient Romans. But we must also consider the exceptional nature of the construction materials. Specifically, how does ancient Roman concrete survive millenia, while often enduring harsh conditions? A team of researchers led by the Massachusetts Institute of Technology have used a handful of analytical techniques to solve the mystery – and the answer can be found in the complex process of “hot mixing” (1).
Previously, the process of slaking – where water is added to lime to form a highly reactive paste – was suspected as the culprit of durability – and the macroscopic lime clasts visible in the mixture were attributed to poor mixing practices. But Admir Masic, lead author of the study, had one nagging question: “If the Romans put so much effort into making an outstanding construction material, following all of the detailed recipes that had been optimized over the course of many centuries, why would they put so little effort into ensuring the production of a well-mixed final product?” (2).
In the study, 2,000-year-old Roman mortar samples from the archaeological site of Privernum, Italy, were subjected to large-area scanning electron microscopy and energy-dispersive x-ray spectroscopy (SEM-EDS), powder X-ray diffraction, and confocal Raman imaging. SEM-EDS revealed the complex chemical composition of the mortar, and found the tiny clasts to be calcium carbonate. Spectroscopic techniques indicated that these were formed via an exothermic reaction – evidence of calcium oxide (quicklime) hydration.
From this, the MIT researchers deduced that Roman concrete was likely made by mixing quicklime directly with pozzolanic material (such as volcanic ash) and water at extremely high temperatures.
“The benefits of hot mixing are twofold. First, when the overall concrete is heated to high temperatures, it allows chemistries that are not possible if you only used slaked lime, producing high-temperature-associated compounds that would not otherwise form.” said Masic in the press release. “Second, this increased temperature significantly reduces curing times since all the reactions are accelerated, allowing for much faster construction.”
The hot mixing process also gives rise to lime clasts with a brittle nanoparticulate architecture that not only preferentially fractures but also enables “self-healing” of those cracks on exposure to more water.
The team hope that their findings will be considered in future cementing formulations to develop more sustainable architecture.
References
- LM Seymour et al., Science Advances, 9 (2023). DOI: 10.1126/sciadv.add1602
- MIT News (2023). Available at: https://bit.ly/3K4Jk8r