Thermal Analysis is Hotter Than Ever
Once a steady workhorse of materials characterization, thermal analysis is now taking center stage in high-impact fields such as batteries, biopolymers, and life sciences. We speak with Yu Cheng, of Waters TA Instruments Division, and Scott Twiddy of additive manufacturing pioneer Inkbit, about how thermal techniques are adapting to meet next-gen material demands.
| 11 min read | Interview
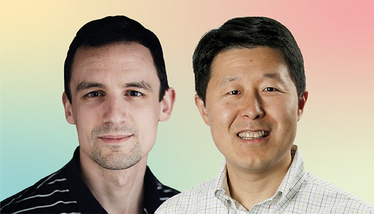
Scott Twiddy and Yu Cheng
Can you tell us about your current role and background?
I'm currently Vice President of R&D and Product Solutions at the TA Instruments Division of Waters Corporation. I’m a scientist by training, with a Ph.D. in chemical and biological engineering from Princeton University, and undergraduate degrees in chemical engineering as well as economics and management from Tsinghua University in Beijing.
Before joining Waters, I led the Metabolic Health business at Nestlé Health Science, where I focused on driving business growth and new product innovation. Earlier in my career, I was an R&D Research Fellow at Merck, supporting 15 investigational new drugs across therapeutic areas such as cardiovascular, diabetes, oncology, and neurology.
I also spent time at McKinsey & Company, where I developed both commercial and product development strategies for major biopharma and biotech companies. At Sanofi and Boehringer Ingelheim, I focused on marketing and commercial operations for major pharmaceutical brands.
In my current role, I'm passionate about solving the big challenges of tomorrow by delivering materials characterization solutions that help accelerate innovations in batteries, advanced materials, and life sciences.
What is your perspective on the major challenges the world is facing today?
At Waters, we're focused on addressing some of the world’s most pressing challenges across key markets. These include polymer recycling and the development of bio-sourced materials to support sustainability goals; innovations in batteries and electric vehicles to drive clean energy solutions; and advancements in pharma and biopharma, where novel therapies and biomaterials are reshaping healthcare. We also work closely with industries like electronics and semiconductors, as well as defense, aerospace, and academic and government research.
Today, the demand for higher-performance and more sustainable materials is greater than ever. While instrument performance – like accuracy, precision, and resolution – remains highly valued, these specifications have become table stakes. What’s increasingly important is delivering instruments that combine high performance with ease of use and reliability.
Thermal analysis has long been a core part of materials characterization. How has it traditionally been used, and how is that evolving?
Thermal analysis is a set of techniques used to study how materials respond to changes in temperature and has been routinely used to assess material performance. It’s been a fundamental tool for understanding phase transitions, thermal stability, and other key material properties. Scientists and manufacturers rely on it to quantify and qualify raw materials, optimize processing conditions, and predict product stability and performance.
Although materials characterization remains at the heart of what we do, the types of materials and their applications have changed significantly. Today, there’s much more focus on areas such as battery materials – where safety, performance, and sustainability are top of mind – as well as life sciences, where drug stability and efficacy are critical. We’re also seeing growing interest in renewable polymers, biopolymers, and other alternatives to petroleum-based materials.
In terms of techniques, while traditional methods such as DSC (differential scanning calorimetry) and TGA (thermogravimetric analysis) continue to be widely used, we’re seeing increasing demand for microcalorimetry. This technique allows for ultra-sensitive measurements of very small heat changes in materials – orders of magnitude more sensitive than traditional DSC. With microcalorimetry, scientists can detect subtle physical transitions or chemical reactions early in the process, which may be missed with other methods.
Although it’s still relatively underutilized, microcalorimetry holds tremendous potential, particularly in high-impact areas like batteries, life sciences, defense, and advanced materials. We see it as an exciting frontier in thermal analysis.
Let’s take rheology as another example. It has traditionally been used to study how materials flow and deform under stress. These measurements are crucial for ensuring successful processing, optimizing product performance, and gaining insight into the microstructure of complex materials. Rheology plays a key role in the development of everything from consumer products to industrial materials.
What’s exciting is how this technique is now being applied in the battery space. We're using rheology to examine battery slurries throughout their lifecycle – from early R&D through to manufacturing and quality control. There’s still a lot to uncover about how these materials behave as batteries are assembled, stored, and used in real-world applications.
Where do you see thermal analysis adding the most value in today’s world?
One of the most exciting areas where we’re seeing thermal analysis make a big impact is in battery material characterization. We’re increasing our focus here – from analyzing raw materials to evaluating entire battery cells – because nearly everything we use today is powered, and more often than not, it's untethered. That means the demand for high-performing, reliable batteries in all shapes and sizes is only going up.
As the industry pushes the limits of what's possible, companies are constantly testing new materials. But to move beyond a “trial and error” approach, they need sophisticated analytical systems that can provide deep insights into material behavior. That’s exactly where analytical technology comes in – to help guide material development with precision and predictability.
Can you share some examples of how TA technology is being used in modern applications?
Absolutely. Professor Stan Whittingham – who received the Nobel Prize in Chemistry for his pioneering work on lithium-ion batteries – recently published a study using both our Differential Scanning Calorimetry (DSC) system and our Battery Cycler Microcalorimeter Solution (BCMS). Professor Whittingham and his team emphasized the importance of evaluating thermal behavior under real operational conditions, not just in static lab setups. BCMS provided accurate measurements of the heat generated by battery cells during charging and discharging cycles – critical data for assessing battery performance and safety.
Another great example comes from one of our collaborators, Inkbit, which is using our recently released ElectroForce Apex 1, a multifunctional mechanical tester, to test the mechanical properties of their 3D printing materials. As additive manufacturing becomes more prevalent, having the right tools to evaluate the performance and durability of printed parts is essential.
How do you work with customers like Inkbit?
Collaboration with customers like Inkbit is absolutely essential to how we innovate. One of our key goals is to get our products into customers’ hands early so we can assess how well the ease-of-use features we’ve built into the instruments are actually delivering in a real lab environment. It's about ensuring that the solutions we provide fit seamlessly into their workflows – because the smoother the integration, the lower the barrier to use.
We also focus on making data collection and analysis as intuitive as possible. It’s not just about generating raw data; it's about making it easy to extract insights. That means designing systems that are user-friendly and don’t require deep statistical expertise to interpret results. When we engage in these kinds of partnerships, we’re not only helping our customers innovate faster – we’re also learning from them in real time, which makes our products better.
You’ve worked across research, business strategy, and marketing. From that diverse experience, what are some of the key lessons you’ve learned about developing and commercializing new products?
Having worked across several industries, I’ve gained a broad perspective that helps me connect dots across sectors. For example, in pharma, you're dealing with high risk and high reward, so there’s a strong emphasis on portfolio and risk management. On the other hand, consumer products companies are masters of consumer insight – they map out the user journey in detail and use that understanding to shape product development.
Some of the most important lessons I’ve learned include the critical role of understanding the “voice of the customer” (VOC). Successful innovation starts with deep insights into unmet needs. The most innovative companies are the ones that find ways to integrate customer input across departments and stay close to their user base throughout the development cycle.
Strong portfolio management is also vital. You have to make tough choices and focus on the innovations that will have the greatest impact. It helps to have separate processes for breakthrough and incremental innovations, because they require different approaches.
Finally, balancing internal and external innovation is key. No one can innovate effectively in a silo. The best innovators are well connected to their field – whether through partnerships, customer engagement, or research collaborations.
Now that you’ve been in the analytical science space for a year, what’s your take on the current state of innovation?
There’s definitely a strong appetite for innovation in analytical science. Customers are looking for more than just improvements in accuracy and precision – they want instruments that are easy to use, that integrate into simpler workflows, and that offer high throughput and automation. There’s also growing interest in smart data handling and accessible insights.
What’s especially exciting is the rise of AI and machine learning. These technologies are opening up entirely new paradigms for discovering and designing materials. Many of our customers are now actively investing in AI and big data strategies, and that presents a major opportunity for us. We need to make sure our instruments are AI-compatible and data-friendly so they can support that next level of innovation.
Chromatography’s 3D-Printed Future
Inkbit’s fabrication technology makes it possible to manufacture complex multi-material structures for fluidic handling applications – such as complete chromatography devices, including both the gel matrix and the surrounding housing
Scott Twiddy is the Head of Materials R&D at Inkbit, an additive manufacturing company that spun out of MIT’s Computer Science and Artificial Intelligence Laboratory (CSAIL). Inkbit was founded following a breakthrough machine vision system for in-line process control, which the team integrated into an inkjet printing platform. Here, he explains how it works, why it matters, and how it could shake up the chromatography world.
How it works
After depositing a layer of resin, our system scans the surface to generate a topographical height map of that surface. This 3D scan is automatically compared to the digital model of the intended layer, and any deviations from the nominal geometry are corrected in real-time by adjusting the next layer. Our scanner operates at high resolution, ensuring precise, high-fidelity printing. We call our process vision-controlled jetting (VCJ).
Beyond precision, through the use of our feedback control system we avoid all contact with the print surface during printing, this allows Inkbit to process materials and chemistries that are challenging, or even impossible, for other additive manufacturing technologies such as stereolithography and other inkjet solutions. So far, we’ve commercialized two distinct resin families: epoxy and thiol-ene polyurethanes. Unlike hybrid acrylate formulations that result in compromises, these are single cure chemistry systems are designed for optimal performance.
Why this matters
Our epoxy formulation, derived from epoxy coatings known for their exceptional chemical resistance, is particularly well-suited for fluidic handling applications. We’ve tested our chemical-resistant epoxy by submerging samples in acetone for months without any degradation. Combined with our strong ability to produce a wide range of structural features, this makes this material family printed on our system ideal for fluidic applications.
Recently, we’ve been focusing on chromatography applications. Right now, we can print housings and manifolds for chromatography systems, and with the right partners, we see a future where we can fabricate the internal gel structure of a chromatography column and the housing of the column as a complete device. This highlights one of the most exciting aspects of Inkbit’s technology: just as an inkjet printer combines CMYK inks, our platform can print multiple materials from different printheads. This enables precise spatial control over mechanical properties within a printed structure, opening up new possibilities in advanced manufacturing.
Partnerships
At Inkbit, we work closely with customers to develop innovative solutions that are not viable with other manufacturing technologies. Our partnership with the TA Instruments Division at Waters equips us with advanced testing capabilities, enabling us to push the boundaries of material performance and process optimization.
For instance, we utilize dynamic mechanical analysis (DMA) and differential scanning calorimetry (DSC) to examine key microstructural features in our multi-material printing, allowing for rapid optimization of printed structures. The recent addition of ElectroForce Apex 1 to our testing suite further enhances our ability to evaluate mechanical performance under real-world conditions, an important factor for many of our customers who prioritize real-world functionality over generic datasheet metrics.